Существует огромное количество типов оснастки, предлагаем их условно разбить на группы: сборочная, транспортировочная, формообразующая и литейная. К сборочным относятся калибры, примерочные шаблоны, держатели инструмента и тд.; к транспортировочной - держатели элементов, блокираторы, запорные механизмы, к формообразующей - штампы для тонкостенного металла, матрицы и пуансоны для листогибочных станков, формы для холодной выкладки композитов и формы для горячей выкладки композитов до 120 или 180 градусов; к литейной мастер модели для выжигания, выплавления или литья «в землю» (литье ХТС).
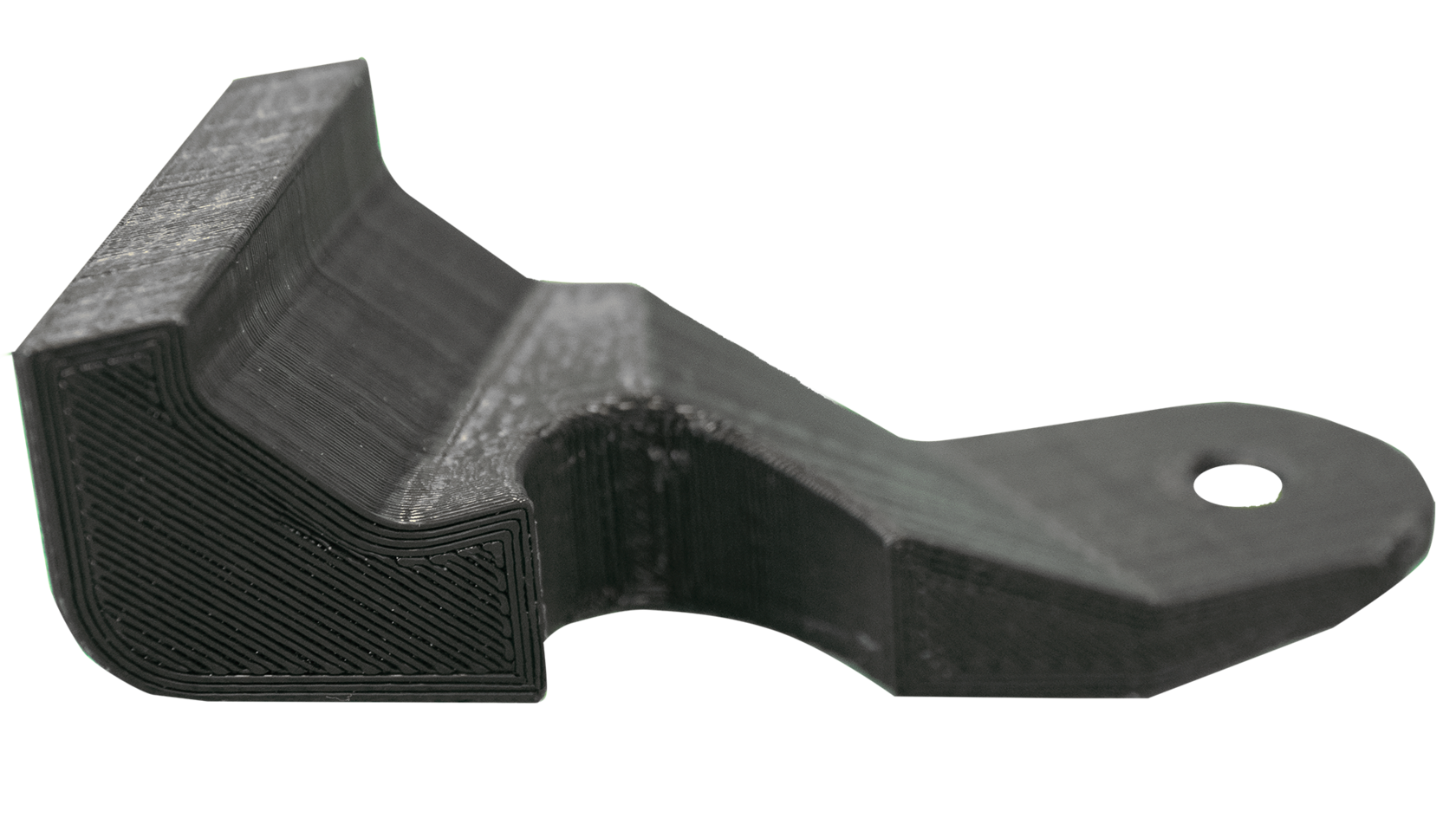
Два основным метода печати подобных изделий — это либо FDM/FFF 3D печать, либо FGF печати с последующей дополнительной механической обработкой. FFF/FDM технология подразумевает печать путем экструзии и послойного наплавления полимерного прутка, FGF – печать методом послойного наплавления гранул. У печати из гранул есть свои плюсы и минусы. Среди плюсов – низкая стоимость сырья и высокая скорость изготовления, однако это влечет за собой один, но довольно существенный минус: низкое качество изделия. Для устранения данного недостатка, а именно выраженной слоистости, детали могут быть подвергнуты механической постобработке (фрезеровочным или токарным станком).
Главные преимущества 3D печати в оснастке – небольшие сроки и низкая стоимость изготовления деталей. Например, для увеличения коэффициента использования материала, при печати из гранул оснастки под ХТС литье, пользователь имеет возможность печатать деталь пустотелой с сетчатым заполнением внутри, чтобы сохранить форму и жесткость. Обычно такую форму делают из десятков листов фанеры или специального пластика. При этом, стоимость 1 кг пластика готовой детали будет такой же, сколько бы стоил пластик под фрезеровку, но с экономией в весе до 50-90% в зависимости от геометрии детали.
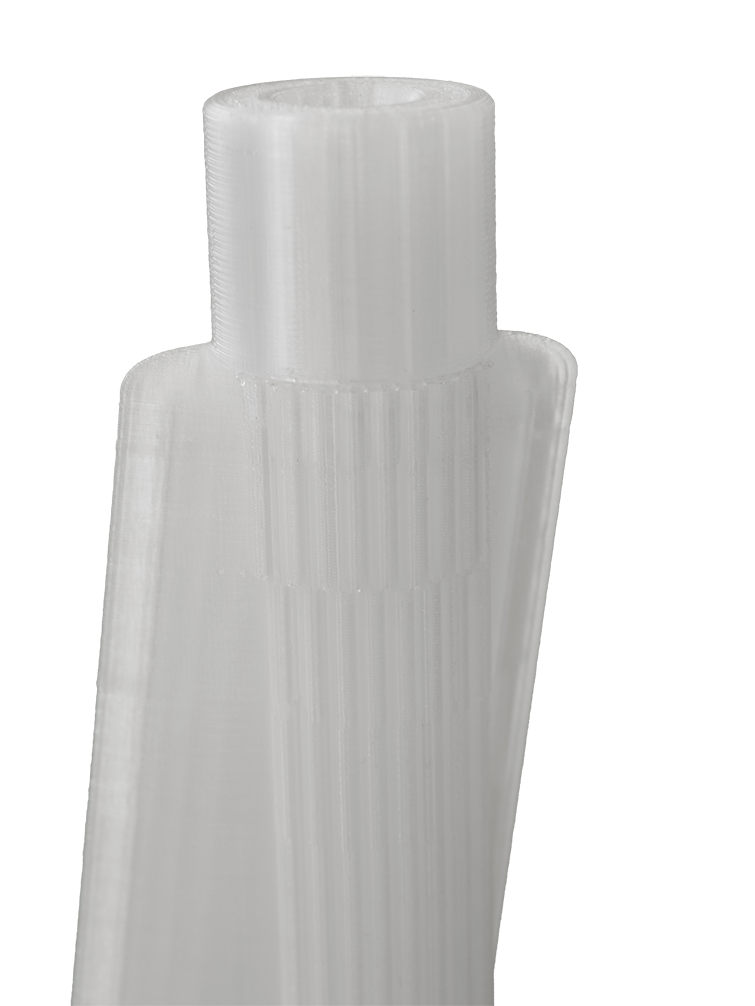
Другой пример: пуансон для выкладки композитов, изготовленный методом классического (субтрактивного) производства будет, в среднем, стоить почти в 10 раз дороже, чем матрица, напечатанная на 3D принтере (даже с постобработкой).
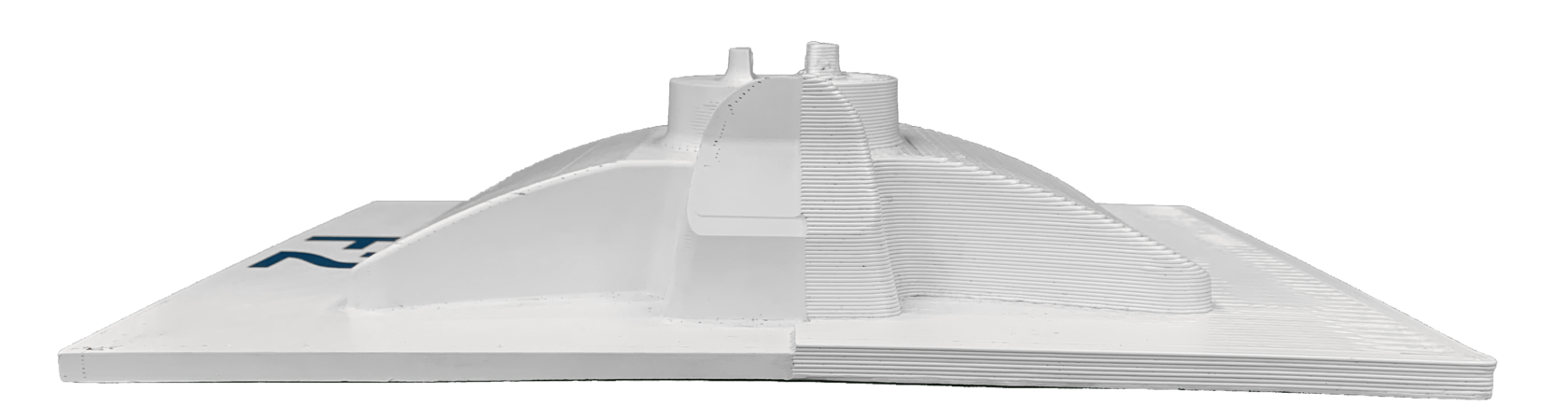
К сожалению, в нашей стране аддитивные технологии долго и медленно входят в производственный процесс из-за устоявшихся принципов многих предприятий, но в последнее время явно наблюдаются положительные тенденции. Так, высокая цена и сложности заказа пуансонов и другой оснастки из-за рубежа все чаще заставляют производства обращать внимание на печатные детали и аддитивное производство.
Изготовление матрицы и пуансона для гибочного пресса по классической технологии (из металла на станках с ЧПУ) для проверки гипотезы займет несколько недель, а оснастка будет стоить несколько сотен тысяч рублей. При наличии гранульного принтера на производстве процесс создания полимерных матрицы и пуансона займет несколько часов, а стоить это будет не более двух тысяч рублей. Такие пуансоны выдерживают до 50 итераций гибки тонкостенного металла, что создает абсолютно новый сценарий изготовления деталей, из-за отсутствия необходимости заказывать дорогостоящий классический пуансон и несколько месяцев ждать его изготовления. Достаточно напечатать деталь за несколько часов, отфрезеровать ее и сразу использовать в технологическом процессе. Это намного сокращает время производства изделий, особенно если задача заключается в проверке той или иной гипотезы или изготовлении мелкой партии.
Печать оснастки – лишь один из примеров использования гибрида аддитивного и субтрактвного производства. Печать гранулами в мировой практике только начинает развиваться, крупные мировые компании переходят с субтрактивного на гибридное производство, которое значительно быстрее и дешевле.