Новый еженедельный дайджест мира АТ от F2 innovations за прошедшую неделю.
Новинки
Fabrisonic представила новый гибридный 3D принтер SonicLayer 1600
Компания Fabrisonic использует в своих принтерах запатентованный процесс ультразвуковой 3D печати - Ultrasonic Additive Manufacturing (UAM). Его суть заключается в последовательном размещении тонких полосок металлической фольги и их приваривании к уже наложенным слоям с помощью ультразвуковых колебаний.
Объем сборки нового 3D принтера SonicLayer 1600 составляет 368 x 368 x 432 мм. Устройство оснащается мощным шпинделем 9 кВт на раме фрезерного центра с ЧПУ среднего размера для обрезки ненужных остатков каждого слоя после ультразвуковой сварки.
Как отмечается в пресс-релизе Fabrisonic: "SonicLayer 1600 - это идеальная платформа для производственных операций, требующих изготовления изделий и устройств, которые предполагают печать разнородных металлов, встраивание датчиков или создание гладких, сложных внутренних каналов и геометрии - или всех трех. SonicLayer 1600 обеспечивает такой уровень возможностей для среднеразмерной платформы с ЧПУ/фрезерным станком, который невозможно найти нигде больше".
Подробнее: https://www.3dpulse.ru/news/promyshlennost/fabrisonic-predstavila-novyi-gibridnyi-3d-printer-soniclayer-1600/
Объем сборки нового 3D принтера SonicLayer 1600 составляет 368 x 368 x 432 мм. Устройство оснащается мощным шпинделем 9 кВт на раме фрезерного центра с ЧПУ среднего размера для обрезки ненужных остатков каждого слоя после ультразвуковой сварки.
Как отмечается в пресс-релизе Fabrisonic: "SonicLayer 1600 - это идеальная платформа для производственных операций, требующих изготовления изделий и устройств, которые предполагают печать разнородных металлов, встраивание датчиков или создание гладких, сложных внутренних каналов и геометрии - или всех трех. SonicLayer 1600 обеспечивает такой уровень возможностей для среднеразмерной платформы с ЧПУ/фрезерным станком, который невозможно найти нигде больше".
Подробнее: https://www.3dpulse.ru/news/promyshlennost/fabrisonic-predstavila-novyi-gibridnyi-3d-printer-soniclayer-1600/
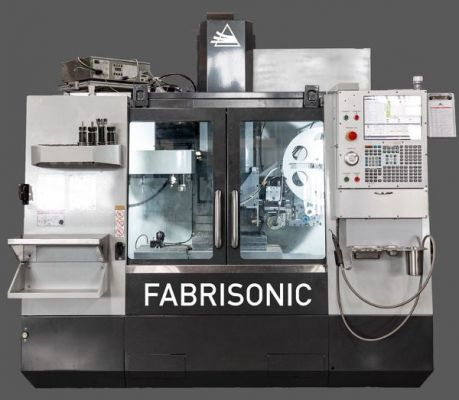
Новый гибридный 3D принтер SonicLayer 1600
NASA разработала новый суперсплав GRX-810
NASA и Университет штата Огайо разработали новый 3D печатный суперсплав — в два раза прочнее, более чем в тысячу раз долговечнее и в два раза устойчивее к окислению по сравнению с современными аналогами. Ввиду способности выдерживать жесткие условия эксплуатации материал планируется применять в аддитивном производстве более надежных и долговечных жаропрочных деталей авиационных и ракетных двигателей.
Новый суперсплав получен после компьютерного термодинамического моделирования в процессе 3D печати методом лазерного порошкового синтеза на подложке. Суперсплав GRX-810 может значительно повысить прочность и ударную вязкость компонентов и деталей, используемых в авиации и космонавтике, считает научный сотрудник Исследовательского центра NASA имени Джона Гленна и соавтор исследования, доктор технических наук Тим Смит.
Подробнее: https://3dtoday.ru/blogs/news3dtoday/nasa-opublikovalo-doklad-po-novomu-supersplavu-grx-810
Новый суперсплав получен после компьютерного термодинамического моделирования в процессе 3D печати методом лазерного порошкового синтеза на подложке. Суперсплав GRX-810 может значительно повысить прочность и ударную вязкость компонентов и деталей, используемых в авиации и космонавтике, считает научный сотрудник Исследовательского центра NASA имени Джона Гленна и соавтор исследования, доктор технических наук Тим Смит.
Подробнее: https://3dtoday.ru/blogs/news3dtoday/nasa-opublikovalo-doklad-po-novomu-supersplavu-grx-810
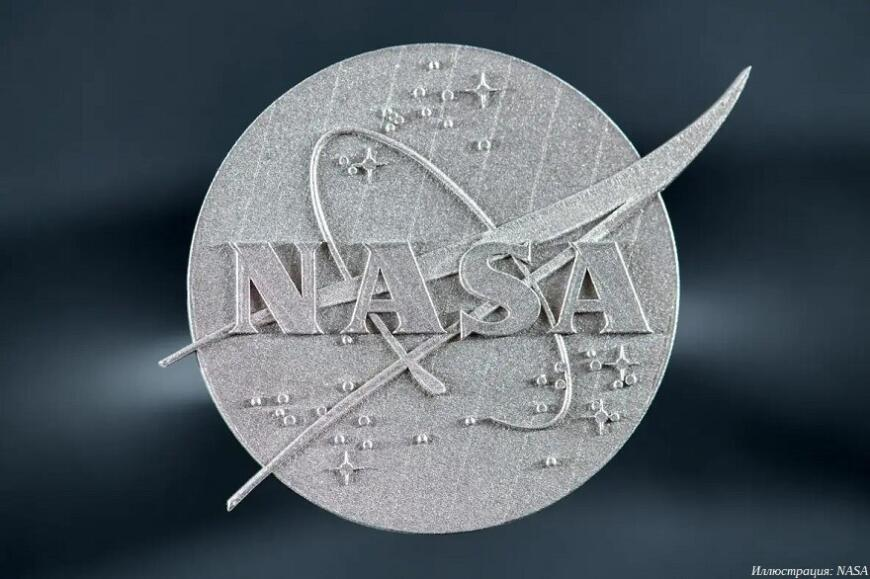
Образец из нового материала
Разработки
Нанкинский университет повышает эффективность разработки компонентов БПЛА с помощью 3D печати
Корпуса дронов сложной формы обычно изготавливаются из акрилонитрилбутадиенстирола (ABS), угленаполненных полиамидов и других инженерных материалов. После ряда сравнительных испытаний сотрудники университета остановились на аддитивном оборудовании компании Intamsys, обеспечивающим высокую точность и производительность при 3D печати инженерными термопластами и композиционными материалами.
Технологии 3D печати помогают специалистам вуза значительно сокращать циклы прототипирования, позволяют быстро изготавливать и проверять прототипы, сокращают временные интервалы от проектирования до получения финальных изделий и тем самым повышают эффективность исследований.
Подробнее: https://additiv-tech.ru/news/nankinskiy-universitet-povyshaet-effektivnost-razrabotki-komponentov-bpla-s-pomoshchyu-3d
Технологии 3D печати помогают специалистам вуза значительно сокращать циклы прототипирования, позволяют быстро изготавливать и проверять прототипы, сокращают временные интервалы от проектирования до получения финальных изделий и тем самым повышают эффективность исследований.
Подробнее: https://additiv-tech.ru/news/nankinskiy-universitet-povyshaet-effektivnost-razrabotki-komponentov-bpla-s-pomoshchyu-3d
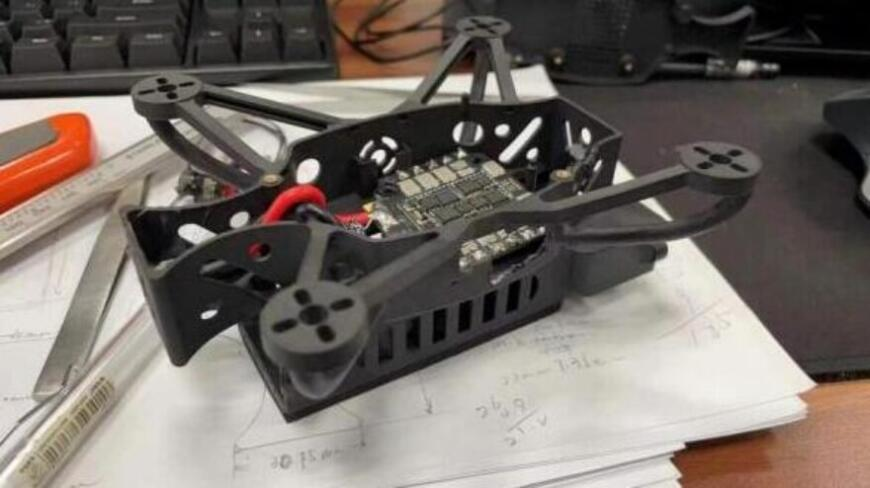
3D печатный корпус дрона
Космонавтика
Космонавты печатают макеты модулей МКС на 3D принтере
Экипаж российского сегмента Международной космической станции приступил к 3D печати макетов всех модулей, чтобы проводить тренировки выходов в открытый космос.
«Например, завтра мы будем контролировать процесс стыковки радиатора к модулю «Наука» и в случае необходимости выдавать команды для корректировки этого процесса. Соответственно, мы отрабатывали взаимодействие с Андреем Федяевым, который будет управлять манипулятором ERA, в привязке к реальным объектам станции. Как раз на этих копиях модулей российского сегмента МКС мы и тренировались. Можно сказать, как у летчиков — «пешим по-летному», — пояснил Дмитрий Петелин.
Подробнее: https://additiv-tech.ru/news/kosmonavty-pechatayut-makety-moduley-mks-na-3d-printere.html
«Например, завтра мы будем контролировать процесс стыковки радиатора к модулю «Наука» и в случае необходимости выдавать команды для корректировки этого процесса. Соответственно, мы отрабатывали взаимодействие с Андреем Федяевым, который будет управлять манипулятором ERA, в привязке к реальным объектам станции. Как раз на этих копиях модулей российского сегмента МКС мы и тренировались. Можно сказать, как у летчиков — «пешим по-летному», — пояснил Дмитрий Петелин.
Подробнее: https://additiv-tech.ru/news/kosmonavty-pechatayut-makety-moduley-mks-na-3d-printere.html
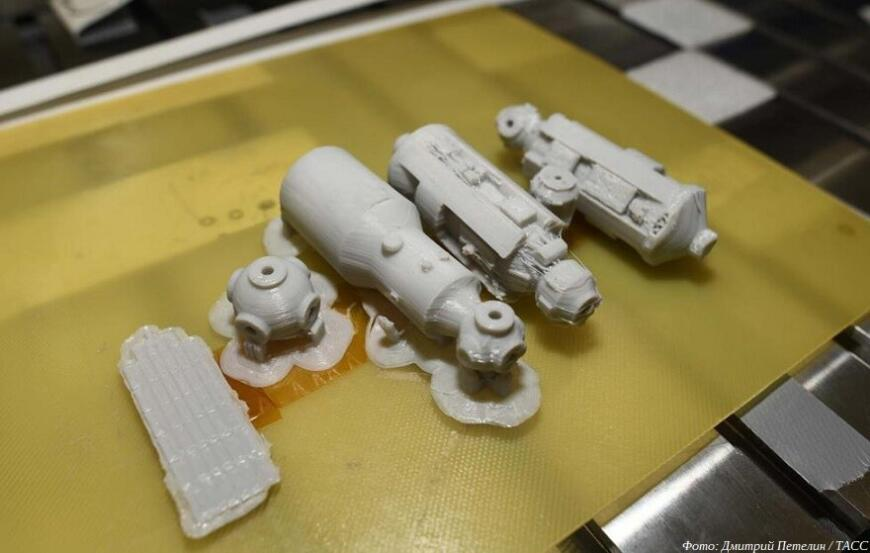
Напечатанные на 3D принтере модули МКС
Медицина
В Зальцбурге проведена революционная операция с использованием 3D печатного черепного имплантата
В Университетской клинике Зальцбурга, Австрия, была успешно применена технология аддитивного производства компании 3D Systems для разработки и производства первого 3D печатного черепного имплантата из PEEK в качестве индивидуального изделия для конкретного пациента.
Штатные клиницисты больницы использовали программное обеспечение D2P компании Oqton для создания 3D моделей на основе снимков КТ пациента и Geomagic Freefrom компании Oqton для проектирования затылочного протеза с учетом особенностей пациента.
Имплантат черепа был напечатан с использованием полиэфирэфиркетона VESTAKEEP i4 3DF компании Evonik на платформе Kumovis R1 компании 3D Systems. Процесс изготовления имплантата диаметром 12 см и толщиной до 3 см занял около 10 часов.
Подробнее: https://www.3dpulse.ru/news/meditsina/v-zaltsburge-provedena-revolyutsionnaya-operatsiya-s-ispolzovaniem-3d-pechatnogo-cherepnogo-implantata/
Штатные клиницисты больницы использовали программное обеспечение D2P компании Oqton для создания 3D моделей на основе снимков КТ пациента и Geomagic Freefrom компании Oqton для проектирования затылочного протеза с учетом особенностей пациента.
Имплантат черепа был напечатан с использованием полиэфирэфиркетона VESTAKEEP i4 3DF компании Evonik на платформе Kumovis R1 компании 3D Systems. Процесс изготовления имплантата диаметром 12 см и толщиной до 3 см занял около 10 часов.
Подробнее: https://www.3dpulse.ru/news/meditsina/v-zaltsburge-provedena-revolyutsionnaya-operatsiya-s-ispolzovaniem-3d-pechatnogo-cherepnogo-implantata/
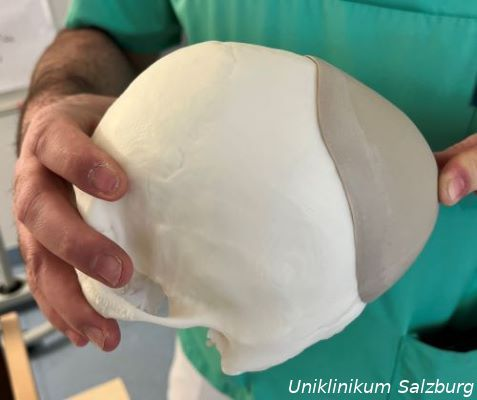
3D печатный черепной имплантат из PEEK