Новый еженедельный дайджест мира АТ от F2 innovations за прошедшую неделю — теперь по пятницам в 15:00!
Медицина
В Германии тестируют напечатанные на 3D принтере лекарства для детей
Университетская клиника Гамбург-Эппендорф (UKE) впервые начала испытания лекарств, изготовленных с помощью 3D печати, на пациентах детского онкологического отделения. Разработка немецких ученых направлена на то, чтобы облегчить прием лекарств.
В рамках совместной исследовательской работы клинической аптеки и детской онкологии UKE проводится оценка предпочтений пациентов между индивидуально дозированными 3D жевательными таблетками и обычными, часто горькими, лекарственными препаратами. Таблетки содержат действующее вещество дексаметазон, которое применяется для профилактики тошноты во время высокодозной химиотерапии при онкологических заболеваниях.
«Мы являемся первой клиникой в Германии, которая самостоятельно разработала 3D печатные лекарства и теперь применяет их для пациентов в детской онкологии в рамках исследования. Мы хотим таким образом обеспечить более точную дозировку лекарств», — объясняет доктор Адрин Дадхах, соруководитель отдела исследований и обучения клинической аптеки UK.
Новая технология разрабатывается в UKE на протяжении трех лет. Предварительное исследование подтвердило возможность интеграции 3D печати в существующий процесс лечения для изготовления индивидуально дозированных медикаментов.
Предполагается, что исследование продлится до 2026 года. В случае успешных результатов, фармацевты и врачи видят перспективы использования 3D печати для комбинирования нескольких действующих веществ в одной таблетке и для индивидуального изготовления лекарств с возможностью корректировки дозировки в процессе лечения.
Подробнее: https://additiv-tech.ru/news/v-germanii-testiruyut-napechatannye-na-3d-printere-lekarstva-dlya-detey.html
В рамках совместной исследовательской работы клинической аптеки и детской онкологии UKE проводится оценка предпочтений пациентов между индивидуально дозированными 3D жевательными таблетками и обычными, часто горькими, лекарственными препаратами. Таблетки содержат действующее вещество дексаметазон, которое применяется для профилактики тошноты во время высокодозной химиотерапии при онкологических заболеваниях.
«Мы являемся первой клиникой в Германии, которая самостоятельно разработала 3D печатные лекарства и теперь применяет их для пациентов в детской онкологии в рамках исследования. Мы хотим таким образом обеспечить более точную дозировку лекарств», — объясняет доктор Адрин Дадхах, соруководитель отдела исследований и обучения клинической аптеки UK.
Новая технология разрабатывается в UKE на протяжении трех лет. Предварительное исследование подтвердило возможность интеграции 3D печати в существующий процесс лечения для изготовления индивидуально дозированных медикаментов.
Предполагается, что исследование продлится до 2026 года. В случае успешных результатов, фармацевты и врачи видят перспективы использования 3D печати для комбинирования нескольких действующих веществ в одной таблетке и для индивидуального изготовления лекарств с возможностью корректировки дозировки в процессе лечения.
Подробнее: https://additiv-tech.ru/news/v-germanii-testiruyut-napechatannye-na-3d-printere-lekarstva-dlya-detey.html
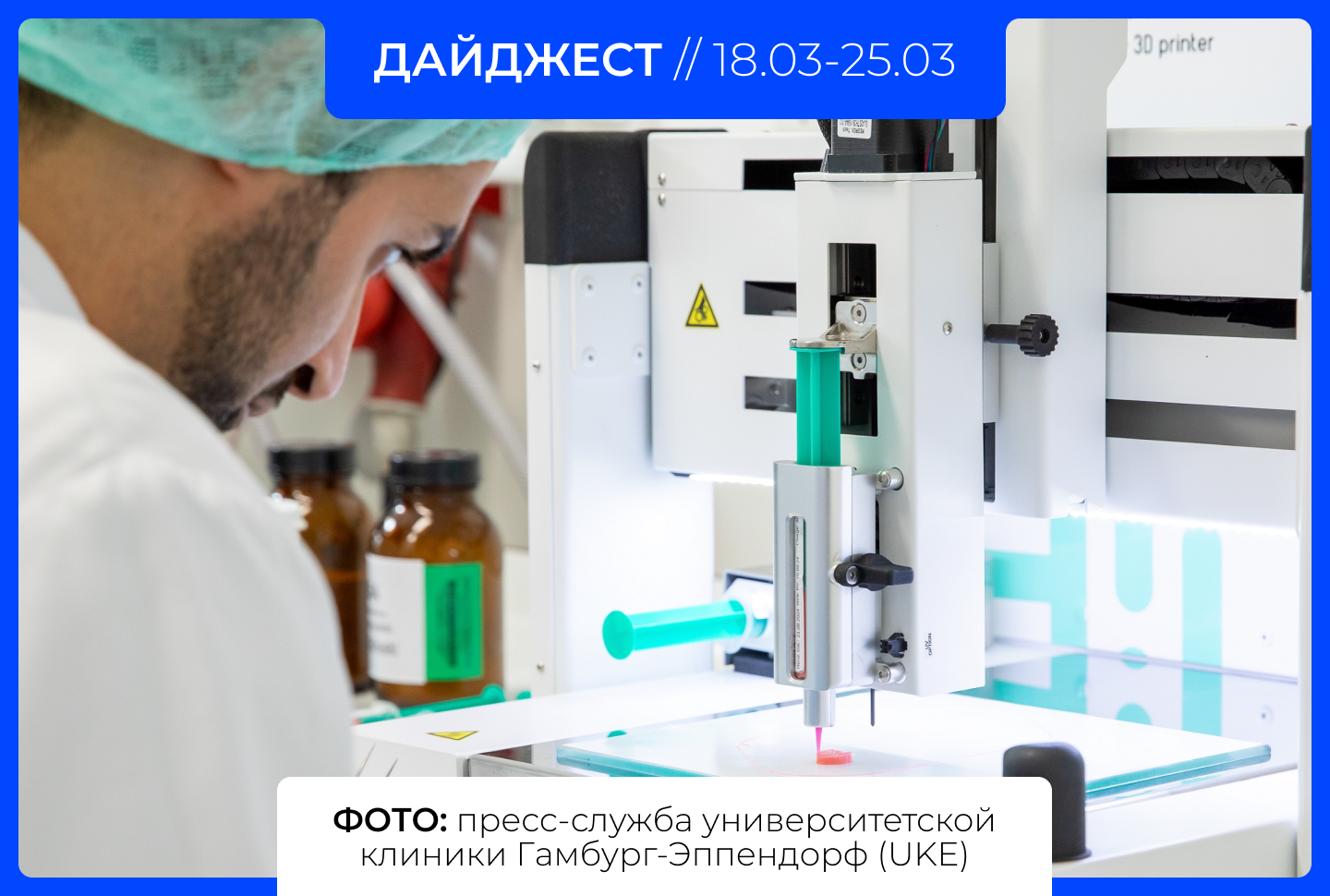
Екатеринбургские врачи применяют 3D печать в нейрохирургии
Врачи Свердловского госпиталя для ветеранов войн успешно провели операцию с использованием аддитивных технологий и поставили на ноги 42-летнего жителя Екатеринбурга. Специалисты отделения гнойной хирургии подготовились к вмешательству с помощью 3D печатной модели поврежденного позвоночника.
Пациент обратился к неврологу с болями в спине. Назначенное консервативное лечение не дало желаемых результатов, дополнительное обследование выявило спондилит грудного отдела позвоночника — заболевание, при котором из-за воспалительного процесса разрушаются позвонки. Прикованного к постели мужчину бригада скорой медицинской помощи доставила в Свердловский госпиталь для ветеранов войн, сообщает пресс-служба Министерства здравоохранения Свердловской области
«С помощью современного программно-аппаратного комплекса удалось спланировать предстоящий план хирургического вмешательства, сделать его безопасным и щадящим для пациента», — рассказал нейрохирург Иван Доценко.
Операция продолжалась четыре с половиной часа. Хирурги удалили поврежденный четвертый позвонок грудного отдела, выполнили фиксацию позвоночного столба с помощью титановой сетки и винтов российского производства. Безопасные траектории проведения винтов рассчитал программно-аппаратный комплекс. В место повреждения имплантировали спейсер: на протяжении четырех недель он будет высвобождать в местные ткани лекарственные препараты в высокой концентрации, ускоряя процесс заживления и снижая нагрузку от воздействия антибиотиков на организм.
Уже в первые сутки после вмешательства пациент отметил значительные изменения: появились движения в ногах, чувствительность. К восстановлению мужчины подключились реабилитологи госпиталя и специалисты отделения лечебной физкультуры. Пациент уже может сидеть без боли, отмечает хорошее восстановление силы в правой ноге, значительное улучшение двигательной функции левой ног и полное исчезновение прежней постоянной боли.
Подробнее: https://3dtoday.ru/blogs/news3dtoday/ekaterinburgskie-vraci-primenyayut-3d-pecat-v-neiroxirurgii
Пациент обратился к неврологу с болями в спине. Назначенное консервативное лечение не дало желаемых результатов, дополнительное обследование выявило спондилит грудного отдела позвоночника — заболевание, при котором из-за воспалительного процесса разрушаются позвонки. Прикованного к постели мужчину бригада скорой медицинской помощи доставила в Свердловский госпиталь для ветеранов войн, сообщает пресс-служба Министерства здравоохранения Свердловской области
«С помощью современного программно-аппаратного комплекса удалось спланировать предстоящий план хирургического вмешательства, сделать его безопасным и щадящим для пациента», — рассказал нейрохирург Иван Доценко.
Операция продолжалась четыре с половиной часа. Хирурги удалили поврежденный четвертый позвонок грудного отдела, выполнили фиксацию позвоночного столба с помощью титановой сетки и винтов российского производства. Безопасные траектории проведения винтов рассчитал программно-аппаратный комплекс. В место повреждения имплантировали спейсер: на протяжении четырех недель он будет высвобождать в местные ткани лекарственные препараты в высокой концентрации, ускоряя процесс заживления и снижая нагрузку от воздействия антибиотиков на организм.
Уже в первые сутки после вмешательства пациент отметил значительные изменения: появились движения в ногах, чувствительность. К восстановлению мужчины подключились реабилитологи госпиталя и специалисты отделения лечебной физкультуры. Пациент уже может сидеть без боли, отмечает хорошее восстановление силы в правой ноге, значительное улучшение двигательной функции левой ног и полное исчезновение прежней постоянной боли.
Подробнее: https://3dtoday.ru/blogs/news3dtoday/ekaterinburgskie-vraci-primenyayut-3d-pecat-v-neiroxirurgii
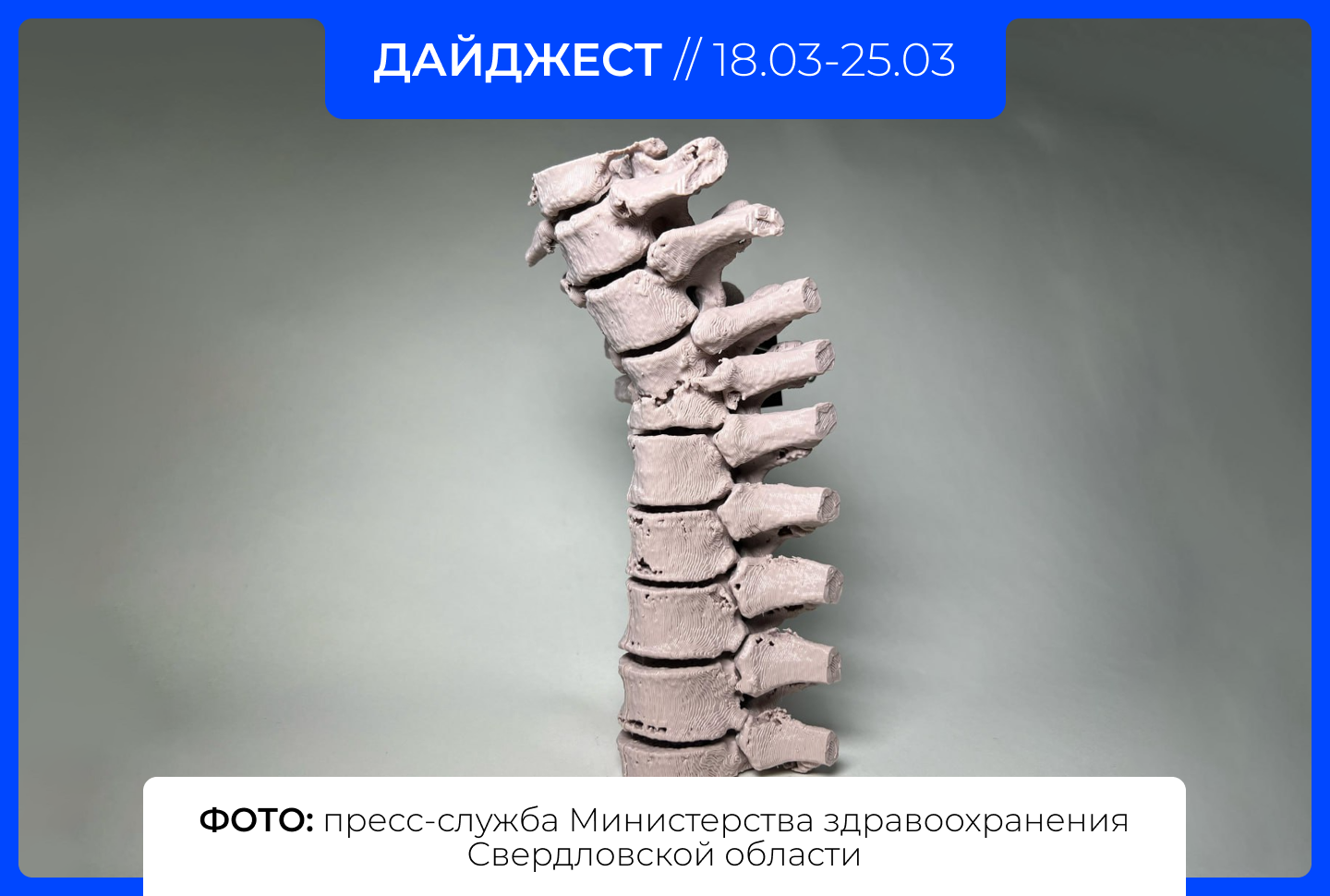
Технологии
В МАИ разработали технологию сверхпрочной 3D печати авиатехники и протезов
Она помогает побороть неравномерность механических свойств напечатанных деталей. Инженеры Московского авиационного института (МАИ) разработали инновационную методику увеличения прочности и срока службы деталей из композитов и полимерных материалов, изготовленных на 3D принтере методом послойного наплавления. Разработка будет полезна в авиастроении, а также изготовлении протезов и ортезов, сообщили ТАСС в пресс-службе вуза.
«С помощью новой методики можно на 30% быстрее изготавливать опытные образцы авиационной техники. Таким образом можно делать разную оснастку: различные пресс-формы для формирования листового металла, приспособления для гибки трубопроводов, кондукторы для сверления, шаблоны для сборки и так далее», – заявил автор проекта, аспирант кафедры технологии производства и эксплуатации двигателей летательных аппаратов МАИ Антон Кузьмин, чьи слова приводятся в сообщении.
Послойное наплавление сегодня является наиболее экономичным и быстрым способом печати в промышленном производстве, прототипировании, бытовом секторе. Технология позволяет использовать большое разнообразие термореактивных материалов с различными физическими и механическими свойствами. Однако у нее есть и недостатки, главный из которых - неравномерная прочность получаемых деталей. С этим и поможет бороться предложенная методика.
«Сегодня в производстве используются методы упрочнения деталей различными растворителями, например, дихлорметаном или ацетоном. Они наносятся на поверхность, из-за чего границы слоев размываются и перемешиваются, что добавляет прочности. Недостатки такого метода в том, что это упрочнение происходит только на поверхности детали. К тому же, некоторая часть растворителя остается в пластике, что при нагревании может приводить к образованию пузырей на поверхности. Мой метод лишен этого недостатка», – утверждает автор проекта.
В МАИ отмечают, что разработанная технология помогает побороть неравномерность механических свойств напечатанных деталей - они становятся одинаково прочными во всех направлениях. После печати деталь утрамбовывается в тонком слое порошка - оксиде магния, затем запекается в печи при температуре, близкой к температуре плавления пластика, после чего выдерживается в течение 1-2 часов. Утрамбованный порошок имитирует литьевую форму, и слои детали сплавляются между собой. Образцы, подверженные такой термической обработке, получаются на 20-30% прочнее исходных деталей, изготовленных при помощи других методик, а после химической обработки они становятся еще и более гладкими.
Подробнее: https://additiv-tech.ru/news/v-mai-razrabotali-tehnologiyu-sverhprochnoy-3d-pechati-aviatehniki-i-protezov.html
«С помощью новой методики можно на 30% быстрее изготавливать опытные образцы авиационной техники. Таким образом можно делать разную оснастку: различные пресс-формы для формирования листового металла, приспособления для гибки трубопроводов, кондукторы для сверления, шаблоны для сборки и так далее», – заявил автор проекта, аспирант кафедры технологии производства и эксплуатации двигателей летательных аппаратов МАИ Антон Кузьмин, чьи слова приводятся в сообщении.
Послойное наплавление сегодня является наиболее экономичным и быстрым способом печати в промышленном производстве, прототипировании, бытовом секторе. Технология позволяет использовать большое разнообразие термореактивных материалов с различными физическими и механическими свойствами. Однако у нее есть и недостатки, главный из которых - неравномерная прочность получаемых деталей. С этим и поможет бороться предложенная методика.
«Сегодня в производстве используются методы упрочнения деталей различными растворителями, например, дихлорметаном или ацетоном. Они наносятся на поверхность, из-за чего границы слоев размываются и перемешиваются, что добавляет прочности. Недостатки такого метода в том, что это упрочнение происходит только на поверхности детали. К тому же, некоторая часть растворителя остается в пластике, что при нагревании может приводить к образованию пузырей на поверхности. Мой метод лишен этого недостатка», – утверждает автор проекта.
В МАИ отмечают, что разработанная технология помогает побороть неравномерность механических свойств напечатанных деталей - они становятся одинаково прочными во всех направлениях. После печати деталь утрамбовывается в тонком слое порошка - оксиде магния, затем запекается в печи при температуре, близкой к температуре плавления пластика, после чего выдерживается в течение 1-2 часов. Утрамбованный порошок имитирует литьевую форму, и слои детали сплавляются между собой. Образцы, подверженные такой термической обработке, получаются на 20-30% прочнее исходных деталей, изготовленных при помощи других методик, а после химической обработки они становятся еще и более гладкими.
Подробнее: https://additiv-tech.ru/news/v-mai-razrabotali-tehnologiyu-sverhprochnoy-3d-pechati-aviatehniki-i-protezov.html
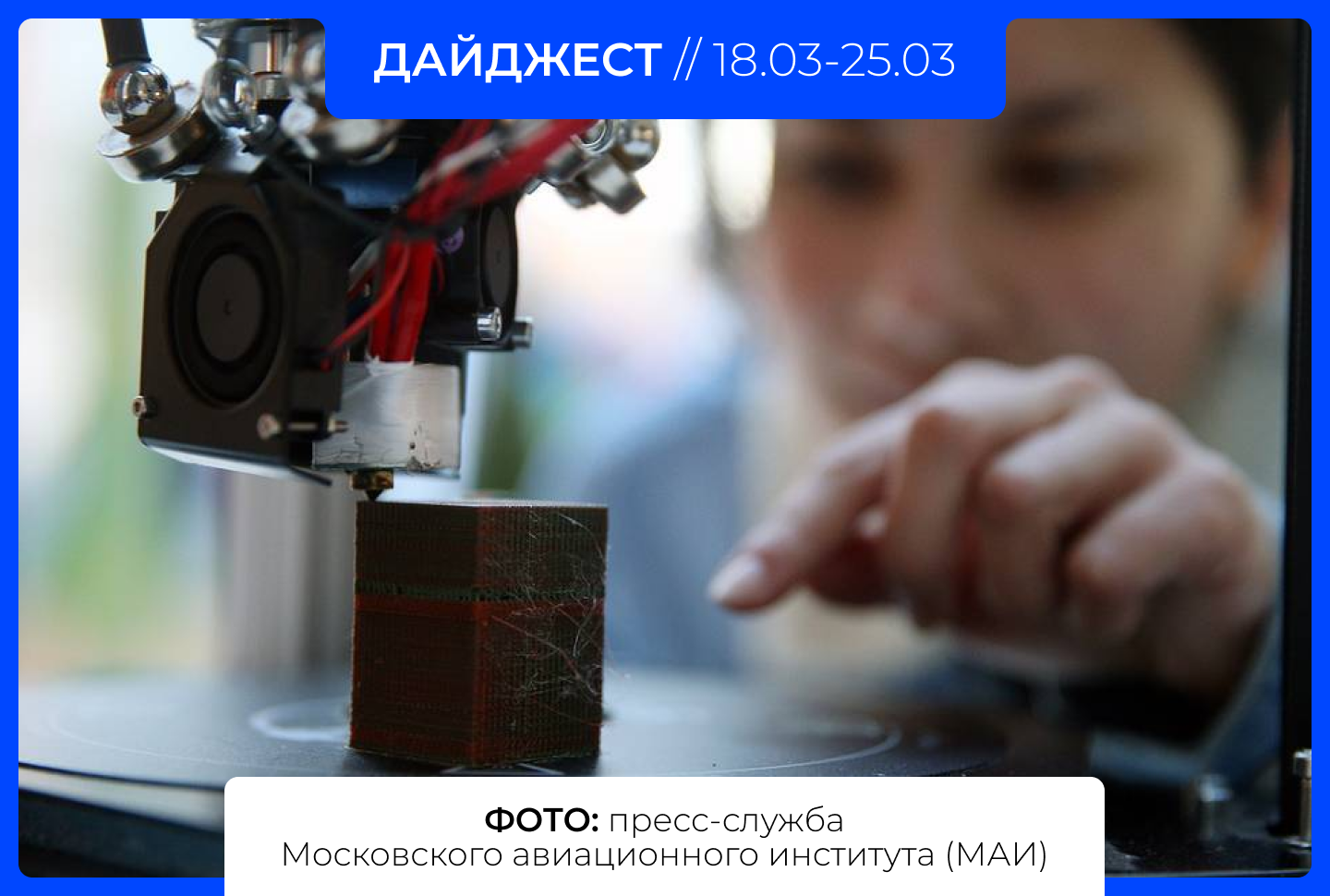
Российский авиапром делает новый шаг к технологической независимости
17 марта стало вехой для российского авиастроения: в Комсомольске-на-Амуре опытный образец самолета «Суперджет» с отечественными двигателями ПД-8 успешно совершил первый полет. Это событие знаменует начало летных испытаний новой силовой установки, что является важным шагом на пути к сертификации полностью российской версии авиалайнера.
Экипаж в составе летчиков-испытателей Дмитрия Деменева, Игоря Гревцева и бортового оператора Максима Грюканова поднял самолет в воздух на 40 минут. За это время машина достигла скорости 500 км/ч и высоты 3000 метров. По словам командира экипажа, программа полета была выполнена безупречно, а двигатели продемонстрировали стабильную работу, включая высокую газодинамическую устойчивость.
Первый заместитель председателя правительства РФ Денис Мантуров отметил, что успешный полет — это значительный шаг к технологической независимости «Суперджета». Для ускорения сертификации к испытаниям планируется подключить третий полностью российский самолет. Государство гарантирует финансовую и ресурсную поддержку авиастроителей.
Двигатель ПД-8, разработанный Объединенной двигателестроительной корпорацией (ОДК), создан с использованием передовых российских материалов и технологий, включая 3D печать. Именно на новом промышленном комплексе ОДК в Москве, строительство которого началось в 2023 году, будут производиться ключевые компоненты для двигателей, включая детали, созданные с помощью аддитивных технологий. Этот комплекс станет одним из крупнейших промышленных центров столицы, объединив мощности Московского машиностроительного предприятия имени В. В. Чернышева и производственного комплекса «Салют».
Новый производственный центр общей площадью более 77 тысяч квадратных метров будет оснащен современным оборудованием для выпуска комплектующих для самолетных и вертолетных двигателей, включая ТВ7-117СТ-01/02, ПД-14, ПД-8, ВК-650В и ВК-1600В. Центр аддитивных технологий, который также разместится на территории комплекса, позволит создавать детали с уникальной геометрией, недоступной для традиционных методов производства.
Генеральный директор ОДК Александр Грачев сообщил, что до конца марта испытателям будут переданы еще два опытных образца ПД-8, а сертификация двигателя ожидается осенью текущего года. «Это результат труда тысяч специалистов, воплотивших ключевую ценность ОДК — общее дело на благо страны», — подчеркнул он.
Первый полет «Суперджета» с двигателем ПД-8 и строительство нового промышленного комплекса в Москве демонстрируют, что Россия последовательно выполняет намеченные планы по достижению технологической независимости в авиастроении. Успешные испытания нового двигателя, созданного с использованием передовых технологий, включая 3D печать, подтверждают готовность страны к импортозамещению.
Строительство крупного производственного центра в Москве, где будут выпускаться ключевые компоненты для авиадвигателей, включая детали для ПД-8, подчеркивает масштабность задач, стоящих перед отраслью. Этот комплекс станет важным звеном в цепочке производства полностью российских авиалайнеров и вертолетов, что особенно актуально в условиях текущих геополитических вызовов.
«После ухода Boeing и Airbus стране нужны свои «крылья». План поставок только по пассажирским самолетам — порядка 500 бортов до 2030 года, плюс обширная вертолетостроительная программа. Задача, поставленная государством, не просто амбициозная, а суперамбициозная. Новый промышленный мегакомплекс в Москве поможет в ее решении», — отметили в пресс-службе ОДК.
Таким образом, Россия не только укрепляет суверенитет авиационной отрасли, но и создает прочную основу для будущего развития, демонстрируя способность выполнять даже самые амбициозные задачи.
Подробнее: https://industry3d.ru/rossijskij-aviaprom-delaet-novyj-shag-k-tehnologicheskoj-nezavisimosti/
Экипаж в составе летчиков-испытателей Дмитрия Деменева, Игоря Гревцева и бортового оператора Максима Грюканова поднял самолет в воздух на 40 минут. За это время машина достигла скорости 500 км/ч и высоты 3000 метров. По словам командира экипажа, программа полета была выполнена безупречно, а двигатели продемонстрировали стабильную работу, включая высокую газодинамическую устойчивость.
Первый заместитель председателя правительства РФ Денис Мантуров отметил, что успешный полет — это значительный шаг к технологической независимости «Суперджета». Для ускорения сертификации к испытаниям планируется подключить третий полностью российский самолет. Государство гарантирует финансовую и ресурсную поддержку авиастроителей.
Двигатель ПД-8, разработанный Объединенной двигателестроительной корпорацией (ОДК), создан с использованием передовых российских материалов и технологий, включая 3D печать. Именно на новом промышленном комплексе ОДК в Москве, строительство которого началось в 2023 году, будут производиться ключевые компоненты для двигателей, включая детали, созданные с помощью аддитивных технологий. Этот комплекс станет одним из крупнейших промышленных центров столицы, объединив мощности Московского машиностроительного предприятия имени В. В. Чернышева и производственного комплекса «Салют».
Новый производственный центр общей площадью более 77 тысяч квадратных метров будет оснащен современным оборудованием для выпуска комплектующих для самолетных и вертолетных двигателей, включая ТВ7-117СТ-01/02, ПД-14, ПД-8, ВК-650В и ВК-1600В. Центр аддитивных технологий, который также разместится на территории комплекса, позволит создавать детали с уникальной геометрией, недоступной для традиционных методов производства.
Генеральный директор ОДК Александр Грачев сообщил, что до конца марта испытателям будут переданы еще два опытных образца ПД-8, а сертификация двигателя ожидается осенью текущего года. «Это результат труда тысяч специалистов, воплотивших ключевую ценность ОДК — общее дело на благо страны», — подчеркнул он.
Первый полет «Суперджета» с двигателем ПД-8 и строительство нового промышленного комплекса в Москве демонстрируют, что Россия последовательно выполняет намеченные планы по достижению технологической независимости в авиастроении. Успешные испытания нового двигателя, созданного с использованием передовых технологий, включая 3D печать, подтверждают готовность страны к импортозамещению.
Строительство крупного производственного центра в Москве, где будут выпускаться ключевые компоненты для авиадвигателей, включая детали для ПД-8, подчеркивает масштабность задач, стоящих перед отраслью. Этот комплекс станет важным звеном в цепочке производства полностью российских авиалайнеров и вертолетов, что особенно актуально в условиях текущих геополитических вызовов.
«После ухода Boeing и Airbus стране нужны свои «крылья». План поставок только по пассажирским самолетам — порядка 500 бортов до 2030 года, плюс обширная вертолетостроительная программа. Задача, поставленная государством, не просто амбициозная, а суперамбициозная. Новый промышленный мегакомплекс в Москве поможет в ее решении», — отметили в пресс-службе ОДК.
Таким образом, Россия не только укрепляет суверенитет авиационной отрасли, но и создает прочную основу для будущего развития, демонстрируя способность выполнять даже самые амбициозные задачи.
Подробнее: https://industry3d.ru/rossijskij-aviaprom-delaet-novyj-shag-k-tehnologicheskoj-nezavisimosti/
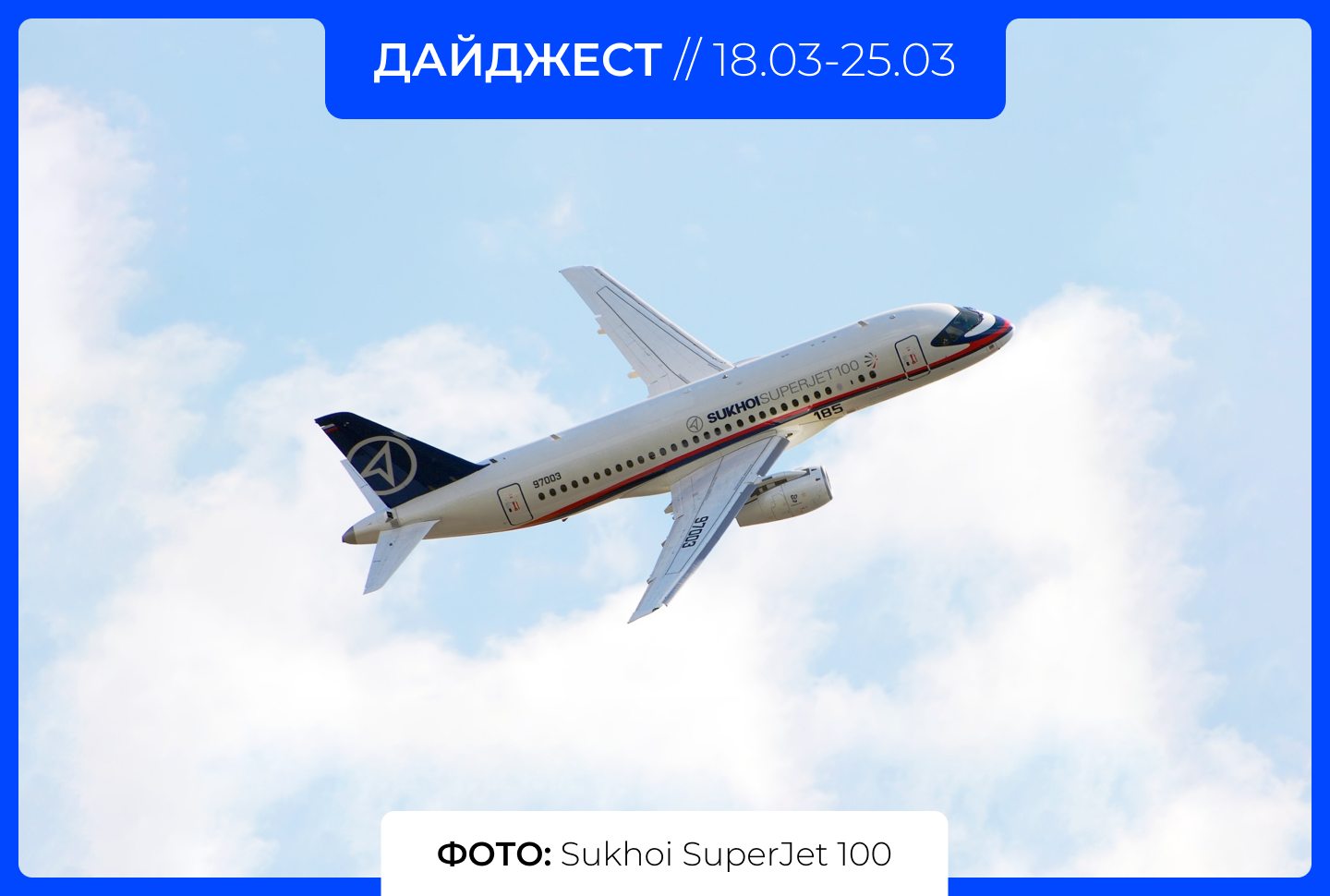