Новый еженедельный дайджест мира АТ от F2 innovations за прошедшую неделю.
Наука
Компания Honda демонстрирует активное использование металлической аддитивной технологии (AТ) в своих внутренних процессах
Японский автопроизводитель официально заявил, что использует металлические AТ в различных целях, в том числе для создания финальных деталей для команды F1 Honda Red Bull. Компания применяет технологию лазерного сплавления порошков (PBF) и системы от Nikon SLM Solutions. Одним из главных преимуществ, полученных Honda, является обширный опыт в оптимизации рабочего процесса AТ и всех параметров процесса.
Honda отмечает, что ее инженеры используют металлические AТ для создания сложных форм, которые невозможно получить с помощью литья или ковки. Компания также подчеркивает, что для эффективного производства требуется значительный опыт, например, в минимизации количества поддерживающего материала и создании форм, которые легко удаляются. Знания в области 3D печати, такие как состояние материала, уровень лазерного излучения, поток инертного газа и размещение изделия на базовой плите, являются ключевыми для повышения качества и эффективности.
По этой причине Honda самостоятельно проектирует и производит несколько металлических аддитивных деталей. Это позволяет компании накапливать опыт, экспериментируя с различными условиями для оптимизации параметров, делая снимки каждого слоя с помощью камеры для проверки состояния плавления, а также контролируя температуру и мощность лазера. Для оптимизации параметров тестовый образец размещается на пластине, и варьируются такие условия, как мощность лазера и скорость сканирования, при этом прочность проверяется с помощью испытаний на растяжение для определения оптимальных значений.
При определении оптимальных значений важно установить параметры лазера так, чтобы шарики (участки, где металлический порошок плавится и затвердевает), образующиеся в каждом слое, перекрывались без зазоров. Если мощность лазера недостаточна, шарики будут слишком маленькими, а расстояние между ними и глубина шарика (толщина слоя) будут недостаточными, что приведет к образованию зазоров. И наоборот, если мощность слишком высока, газ, выделяющийся из расплавленной зоны во время лазерного облучения, не сможет полностью выйти и останется внутри.
Производительность также улучшилась. При переходе от моделирующей машины с небольшой областью построения, используемой на этапе прототипирования, к 3D принтеру с большой областью построения для изготовления конечного продукта, чем больше область построения, тем более она подвержена внешним помехам. Это связано с тем, что в областях на подветренной стороне, где скорость потока инертного газа низкая, недостаточно возможности удалять дым, образующийся при плавлении металла, и брызги расплавленного металла, что приводит к проблемам с моделированием на подветренной стороне. Для решения этой проблемы используется высокоскоростная камера для проверки состояния удаления брызг для каждого слоя. Причина проблемы определяется путем сравнения с распределением скорости ветра с использованием датчика скорости ветра. Оптимизируя скорость ветра, устанавливаются условия для высокого качества во всей области построения.
Металлический процесс PBF состоит из повторяющейся лазерной сварки каждые несколько десятков микрон, что делает деталь склонной к деформации. Традиционно деталь создавалась и измерялась, а параметры корректировались на основе данных измерений. Этот процесс повторялся для повышения точности размеров. Однако этот метод требует времени и не позволяет быстро наладить производство. Поэтому была принята технология симуляции прогнозирования деформации для сокращения проб и ошибок. Внедрив методы деформации, которые хорошо поддаются симуляции, в конструкцию, можно оптимизировать положение модели и форму поддержек, что позволяет быстро создавать модели с высокой точностью размеров.
3D-печать деталей для F1 (поршни, корпуса турбин)
Одним из примеров применения технологии металлической AТ являются детали силового агрегата для автомобилей F1. Honda поставляет двигатели для текущего чемпиона мира, пилота Макса Ферстаппена (Red Bull Racing). Используя технологию металлических AТ, Honda может быстро реагировать на изменения спецификаций, включая сложные тонкостенные формы, которые невозможно было реализовать с помощью традиционных методов производства, что позволяет сократить время производства и снизить затраты.
Поршень, который ранее изготавливался из кованого алюминия, был заменен на стальной, напечатанный на 3D принтере, чтобы придать ему прочность, необходимую для выдерживания увеличения давления сгорания, связанного с прогрессом в разработке. Поскольку сталь имеет более высокую плотность, чем алюминий, она обычно тяжелее. Однако благодаря применению технологии металлических AТ удалось сделать деталь легче, чем при использовании традиционных методов.
Еще одним примером являются корпуса турбин. Они изготавливаются из «инконеля», жаропрочного никелевого сплава, и ранее производились методом точного литья. Корпуса турбин больше поршней и имеют тонкостенные участки, поэтому деформация была серьезной проблемой при производстве. Инженеры Honda успешно разработали эффективную технологию производства поршней и корпусов турбин с использованием металлических AТ. Соответствуя строгим стандартам размеров, они также значительно сократили затраты и время производства. Эти детали были внедрены в середине сезона 2020 года и внесли вклад в победу в том году.
Подробнее: https://www.voxelmatters.com/honda-shows-off-heavy-internal-use-of-metal-am/
Honda отмечает, что ее инженеры используют металлические AТ для создания сложных форм, которые невозможно получить с помощью литья или ковки. Компания также подчеркивает, что для эффективного производства требуется значительный опыт, например, в минимизации количества поддерживающего материала и создании форм, которые легко удаляются. Знания в области 3D печати, такие как состояние материала, уровень лазерного излучения, поток инертного газа и размещение изделия на базовой плите, являются ключевыми для повышения качества и эффективности.
По этой причине Honda самостоятельно проектирует и производит несколько металлических аддитивных деталей. Это позволяет компании накапливать опыт, экспериментируя с различными условиями для оптимизации параметров, делая снимки каждого слоя с помощью камеры для проверки состояния плавления, а также контролируя температуру и мощность лазера. Для оптимизации параметров тестовый образец размещается на пластине, и варьируются такие условия, как мощность лазера и скорость сканирования, при этом прочность проверяется с помощью испытаний на растяжение для определения оптимальных значений.
При определении оптимальных значений важно установить параметры лазера так, чтобы шарики (участки, где металлический порошок плавится и затвердевает), образующиеся в каждом слое, перекрывались без зазоров. Если мощность лазера недостаточна, шарики будут слишком маленькими, а расстояние между ними и глубина шарика (толщина слоя) будут недостаточными, что приведет к образованию зазоров. И наоборот, если мощность слишком высока, газ, выделяющийся из расплавленной зоны во время лазерного облучения, не сможет полностью выйти и останется внутри.
Производительность также улучшилась. При переходе от моделирующей машины с небольшой областью построения, используемой на этапе прототипирования, к 3D принтеру с большой областью построения для изготовления конечного продукта, чем больше область построения, тем более она подвержена внешним помехам. Это связано с тем, что в областях на подветренной стороне, где скорость потока инертного газа низкая, недостаточно возможности удалять дым, образующийся при плавлении металла, и брызги расплавленного металла, что приводит к проблемам с моделированием на подветренной стороне. Для решения этой проблемы используется высокоскоростная камера для проверки состояния удаления брызг для каждого слоя. Причина проблемы определяется путем сравнения с распределением скорости ветра с использованием датчика скорости ветра. Оптимизируя скорость ветра, устанавливаются условия для высокого качества во всей области построения.
Металлический процесс PBF состоит из повторяющейся лазерной сварки каждые несколько десятков микрон, что делает деталь склонной к деформации. Традиционно деталь создавалась и измерялась, а параметры корректировались на основе данных измерений. Этот процесс повторялся для повышения точности размеров. Однако этот метод требует времени и не позволяет быстро наладить производство. Поэтому была принята технология симуляции прогнозирования деформации для сокращения проб и ошибок. Внедрив методы деформации, которые хорошо поддаются симуляции, в конструкцию, можно оптимизировать положение модели и форму поддержек, что позволяет быстро создавать модели с высокой точностью размеров.
3D-печать деталей для F1 (поршни, корпуса турбин)
Одним из примеров применения технологии металлической AТ являются детали силового агрегата для автомобилей F1. Honda поставляет двигатели для текущего чемпиона мира, пилота Макса Ферстаппена (Red Bull Racing). Используя технологию металлических AТ, Honda может быстро реагировать на изменения спецификаций, включая сложные тонкостенные формы, которые невозможно было реализовать с помощью традиционных методов производства, что позволяет сократить время производства и снизить затраты.
Поршень, который ранее изготавливался из кованого алюминия, был заменен на стальной, напечатанный на 3D принтере, чтобы придать ему прочность, необходимую для выдерживания увеличения давления сгорания, связанного с прогрессом в разработке. Поскольку сталь имеет более высокую плотность, чем алюминий, она обычно тяжелее. Однако благодаря применению технологии металлических AТ удалось сделать деталь легче, чем при использовании традиционных методов.
Еще одним примером являются корпуса турбин. Они изготавливаются из «инконеля», жаропрочного никелевого сплава, и ранее производились методом точного литья. Корпуса турбин больше поршней и имеют тонкостенные участки, поэтому деформация была серьезной проблемой при производстве. Инженеры Honda успешно разработали эффективную технологию производства поршней и корпусов турбин с использованием металлических AТ. Соответствуя строгим стандартам размеров, они также значительно сократили затраты и время производства. Эти детали были внедрены в середине сезона 2020 года и внесли вклад в победу в том году.
Подробнее: https://www.voxelmatters.com/honda-shows-off-heavy-internal-use-of-metal-am/
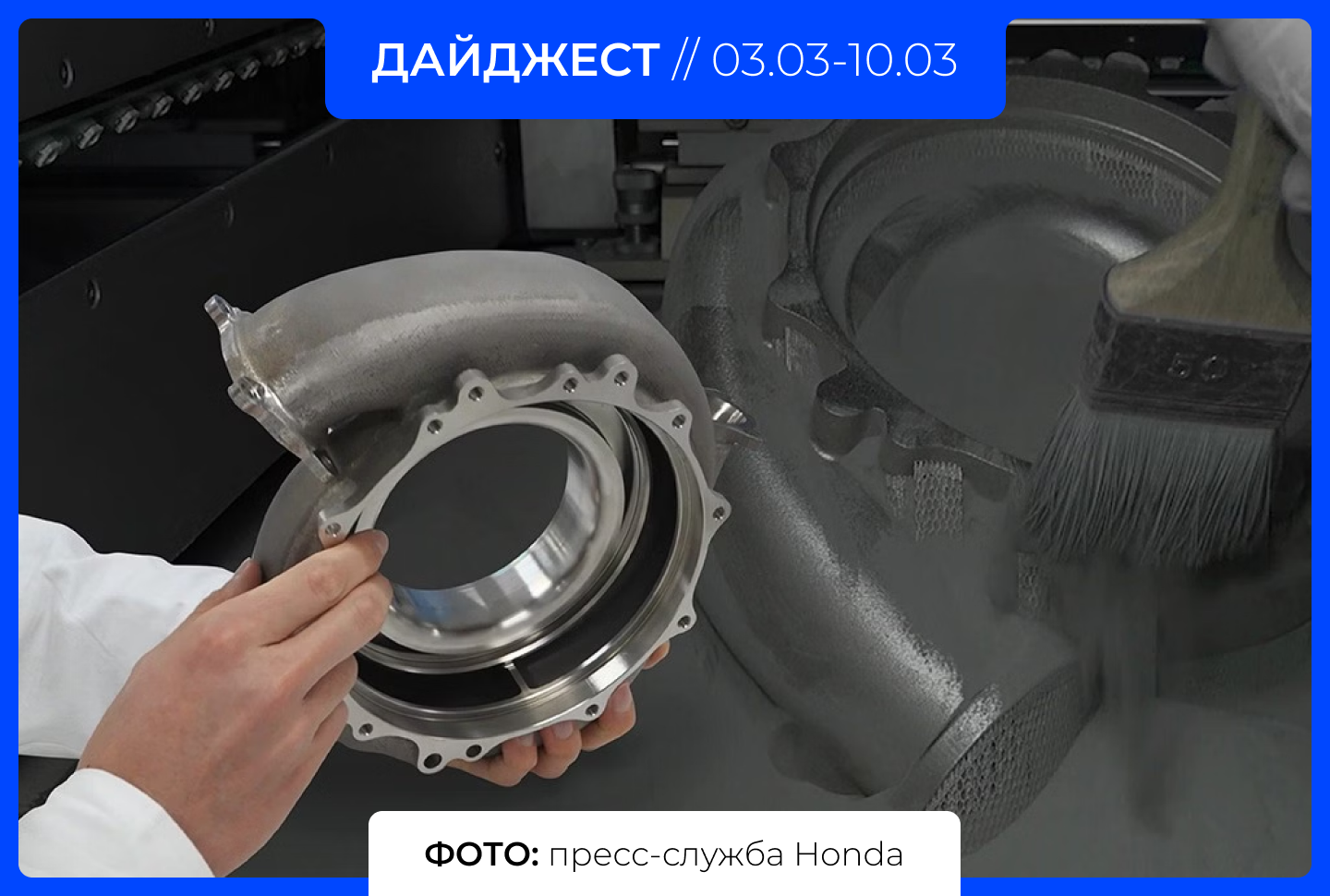
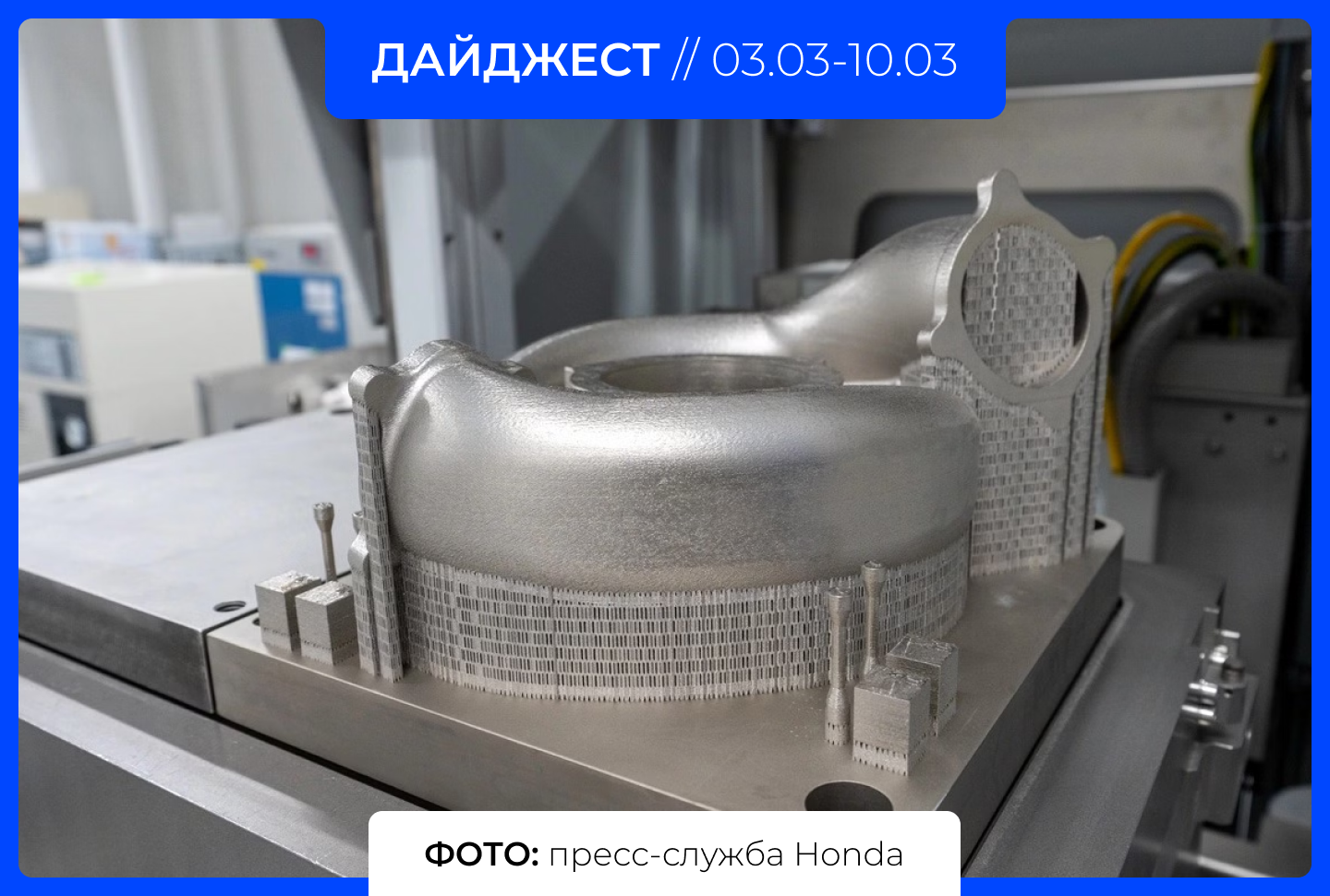
ОДК отгрузила первую партию серийных авиадвигателей ПД-14
Объединенная двигателестроительная корпорация Ростеха передала первую партию серийных авиационных двигателей ПД-14 для установки на среднемагистральный пассажирский самолет поколения МС-21. ПД-14 — первый авиационный двигатель, разработанный в России в постсоветский период и первый отечественный авиадвигатель, использующий 3D печатные компоненты.
При работе над силовой установкой было разработаны и внедрены шестнадцать критических технологий. Специально для ПД-14 изготовлены полые лопатки вентилятора двигателя из титана, созданы новые материалы и покрытия.
«ПД-14 — это прорыв российского двигателестроения. Он стал первым турбовентиляторным двигателем такого уровня, произведенным в современной России. В этот проект вовлечены ведущие предприятия Ростеха, а также десятки организаций из смежных отраслей и научных институтов. Сегодня наши авиастроители и двигателисты делают все возможное для скорейшего проведения сертификационных испытаний импортозамещенного МС-21. Кроме того, на авиазаводах сформирован задел по планерам, идет производство силовых установок, бортовой электроники. Все это необходимо для скорейшего запуска серийного производства самолетов после завершения всех испытаний. Ввиду сжатых сроков сборка серийных лайнеров, разработка и производство комплектующих и бортовых систем, а также испытательные полеты опытных машин ведутся одновременно», — сообщила пресс-служба Ростеха.
В 2022 году Ростех сообщил о запуске серийного аддитивного производства компонентов ПД-14 на мощностях производственного комплекса «Салют» Объединенной двигателестроительной корпорации.
«Для изготовления комплектующих двигателя ПД-14 используются самые современные технологии — тонкостенное литье, аддитивные и роботизированные технологии. Благодаря их применению толщину стенок корпуса удалось уменьшить на 25%, снизить металлоемкость штамповок до 30%, а трудоемкость изготовления узла — на 25–35%, при этом улучшить эксплуатационные характеристики изделий», — рассказал главный инженер комплекса «Салют» Юрий Нуртдинов.
На основе ПД-14 создан и проходит испытания авиадвигатель ПД-8, предназначенный для эксплуатации на «Суперджетах» SJ-100, также ведутся работы над двигателями сверхбольшой тяги ПД-35.
Подробнее: https://3dtoday.ru/blogs/news3dtoday/odk-otgruzila-pervuyu-partiyu-seriinyx-aviadvigatelei-pd-14
При работе над силовой установкой было разработаны и внедрены шестнадцать критических технологий. Специально для ПД-14 изготовлены полые лопатки вентилятора двигателя из титана, созданы новые материалы и покрытия.
«ПД-14 — это прорыв российского двигателестроения. Он стал первым турбовентиляторным двигателем такого уровня, произведенным в современной России. В этот проект вовлечены ведущие предприятия Ростеха, а также десятки организаций из смежных отраслей и научных институтов. Сегодня наши авиастроители и двигателисты делают все возможное для скорейшего проведения сертификационных испытаний импортозамещенного МС-21. Кроме того, на авиазаводах сформирован задел по планерам, идет производство силовых установок, бортовой электроники. Все это необходимо для скорейшего запуска серийного производства самолетов после завершения всех испытаний. Ввиду сжатых сроков сборка серийных лайнеров, разработка и производство комплектующих и бортовых систем, а также испытательные полеты опытных машин ведутся одновременно», — сообщила пресс-служба Ростеха.
В 2022 году Ростех сообщил о запуске серийного аддитивного производства компонентов ПД-14 на мощностях производственного комплекса «Салют» Объединенной двигателестроительной корпорации.
«Для изготовления комплектующих двигателя ПД-14 используются самые современные технологии — тонкостенное литье, аддитивные и роботизированные технологии. Благодаря их применению толщину стенок корпуса удалось уменьшить на 25%, снизить металлоемкость штамповок до 30%, а трудоемкость изготовления узла — на 25–35%, при этом улучшить эксплуатационные характеристики изделий», — рассказал главный инженер комплекса «Салют» Юрий Нуртдинов.
На основе ПД-14 создан и проходит испытания авиадвигатель ПД-8, предназначенный для эксплуатации на «Суперджетах» SJ-100, также ведутся работы над двигателями сверхбольшой тяги ПД-35.
Подробнее: https://3dtoday.ru/blogs/news3dtoday/odk-otgruzila-pervuyu-partiyu-seriinyx-aviadvigatelei-pd-14
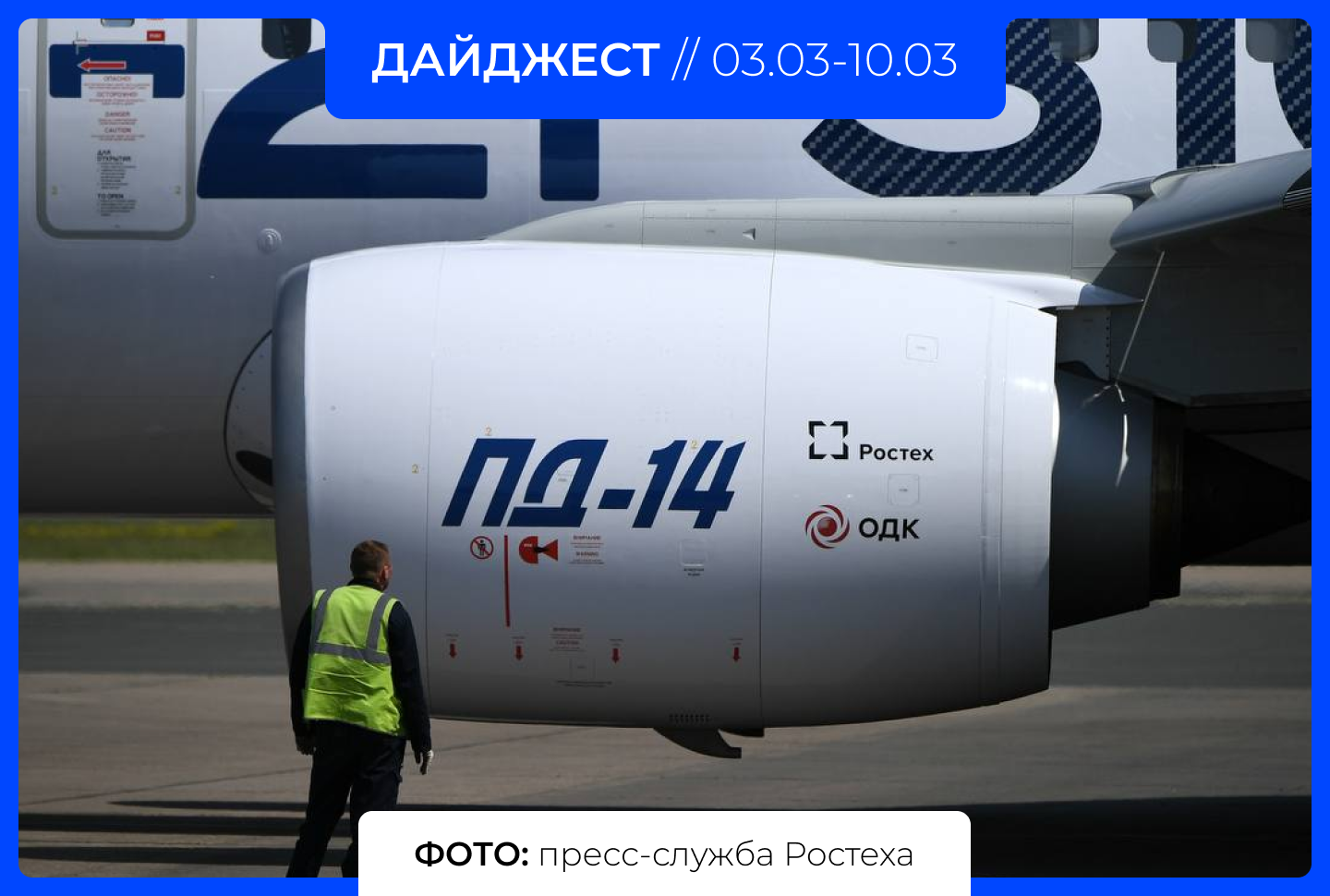
Ростех запустит серийное производство 3D печатных бионических протезов ног
Московское производственное объединение разработало бионический коленный модуль «Комета» для протезирования нижних конечностей. Протез имеет изготовленную на 3D принтере несущую конструкцию из прочного сплава и встроенный микропроцессор для управления движениями в разных режимах ходьбы.
Одной зарядки протеза хватает на десять дней работы, что превосходит показатели аналогичных конкурентных изделий, утверждает пресс-служба государственной корпорации «Ростех». Завершающие испытания протез прошел в конце прошлого года. Пожелания испытателей, опробовавших протезы в повседневной жизни, учтены в итоговой конструкции изделия. В серийное производство новый модуль будет запущен в первом квартале 2025 года.
«С этим протезом я могу ходить, спускаться и подниматься по лестницам, выполнять любые повседневные задачи, танцевать и даже заниматься спортом, например прыгать с парашютом, что я с удовольствием и делаю», — рассказала Ольга Ливерова, принявшая участие в испытаниях.
Корпус протеза изготовлен методом 3D печати из высокопрочного и стойкого к коррозии сплава российского производства. Встроенный микропроцессор осуществляет сбор и обработку данных в режиме реального времени со скоростью более тысячи операций в секунду. Нейросеть предсказывает ритм и рисунок ходьбы, что позволяет использовать протез в различных вариантах — от спокойного до быстрого шага.
Подробнее: https://3dtoday.ru/blogs/news3dtoday/rostex-zapustit-seriinoe-proizvodstvo-3d-pecatnyx-bioniceskix-protezov-nog
Одной зарядки протеза хватает на десять дней работы, что превосходит показатели аналогичных конкурентных изделий, утверждает пресс-служба государственной корпорации «Ростех». Завершающие испытания протез прошел в конце прошлого года. Пожелания испытателей, опробовавших протезы в повседневной жизни, учтены в итоговой конструкции изделия. В серийное производство новый модуль будет запущен в первом квартале 2025 года.
«С этим протезом я могу ходить, спускаться и подниматься по лестницам, выполнять любые повседневные задачи, танцевать и даже заниматься спортом, например прыгать с парашютом, что я с удовольствием и делаю», — рассказала Ольга Ливерова, принявшая участие в испытаниях.
Корпус протеза изготовлен методом 3D печати из высокопрочного и стойкого к коррозии сплава российского производства. Встроенный микропроцессор осуществляет сбор и обработку данных в режиме реального времени со скоростью более тысячи операций в секунду. Нейросеть предсказывает ритм и рисунок ходьбы, что позволяет использовать протез в различных вариантах — от спокойного до быстрого шага.
Подробнее: https://3dtoday.ru/blogs/news3dtoday/rostex-zapustit-seriinoe-proizvodstvo-3d-pecatnyx-bioniceskix-protezov-nog
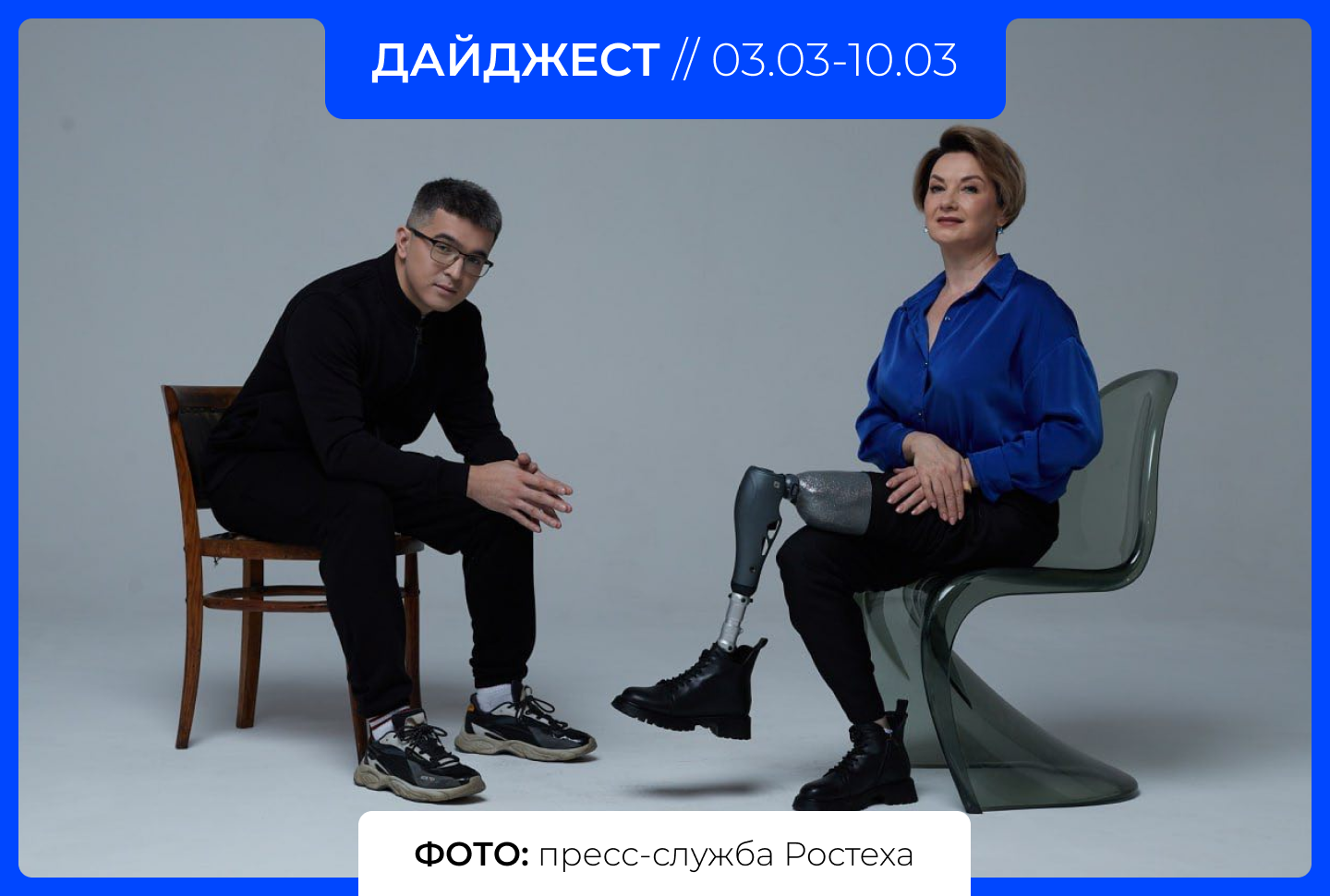