Новый еженедельный дайджест мира АТ от F2 innovations за прошедшую неделю.
Наука
В СамГМУ разработаны аллогенные биоматериалы для 3D биопечати
Ученые Самарского государственного медицинского университета разработали линейку авторских гидрогелей и биочернил для 3D биопечати хрящевых и костных тканей, кожи и слизистых оболочек в реконструктивно-регенеративной медицине. Ученые считают, что эта технология откроет новую эру персонализированной медицины, в которой поврежденные ткани будут не просто замещаться, а естественным образом восстанавливаться.
Материалы разработаны в Самарском банке тканей НИИ «БиоТех» СамГМУ по запатентованной технологии «Лиопласт», сообщает пресс-служба вуза. Биочернила и гидрогели предназначены для создания персонализированных решений в медицине. Ученые разрабатывают отечественные биопродукты для восстановления покровных, опорных и соединительных тканей. 3D биопечать может быть интегрирована в клиническую практику для лечения пациентов.
В травматологии с помощью таких материалов врачи смогут восстанавливать сложные переломы, заполняя дефекты костей персонализированными биопечатными имплантатами, которые ускоряют заживление и снижают риск отторжения. В ортопедии технология позволит создавать анатомически точные хрящевые конструкты для суставов, замедляя развитие артроза у пациентов с дегенеративными заболеваниями. В стоматологии станет возможной 3D печать биоактивных мембран для направленной регенерации тканей при лечении пародонтита или восстановлении утраченных участков костной ткани и слизистых оболочек. В офтальмологии биочернила помогут выращивать трансплантаты роговицы или конъюнктивы для пациентов с ожогами и травмами глаз, возвращая им зрение без риска иммунного отклика.
Главная особенность аллогенных биоматериалов — высокая биосовместимость, минимизирующая риск отторжения. Это выгодно отличает их от ксеногенных и синтетических аналогов.
Подробнее: https://3dtoday.ru/blogs/news3dtoday/v-samgmu-razrabotany-allogennye-biomaterialy-dlya-3d-biopecati
Материалы разработаны в Самарском банке тканей НИИ «БиоТех» СамГМУ по запатентованной технологии «Лиопласт», сообщает пресс-служба вуза. Биочернила и гидрогели предназначены для создания персонализированных решений в медицине. Ученые разрабатывают отечественные биопродукты для восстановления покровных, опорных и соединительных тканей. 3D биопечать может быть интегрирована в клиническую практику для лечения пациентов.
В травматологии с помощью таких материалов врачи смогут восстанавливать сложные переломы, заполняя дефекты костей персонализированными биопечатными имплантатами, которые ускоряют заживление и снижают риск отторжения. В ортопедии технология позволит создавать анатомически точные хрящевые конструкты для суставов, замедляя развитие артроза у пациентов с дегенеративными заболеваниями. В стоматологии станет возможной 3D печать биоактивных мембран для направленной регенерации тканей при лечении пародонтита или восстановлении утраченных участков костной ткани и слизистых оболочек. В офтальмологии биочернила помогут выращивать трансплантаты роговицы или конъюнктивы для пациентов с ожогами и травмами глаз, возвращая им зрение без риска иммунного отклика.
Главная особенность аллогенных биоматериалов — высокая биосовместимость, минимизирующая риск отторжения. Это выгодно отличает их от ксеногенных и синтетических аналогов.
Подробнее: https://3dtoday.ru/blogs/news3dtoday/v-samgmu-razrabotany-allogennye-biomaterialy-dlya-3d-biopecati
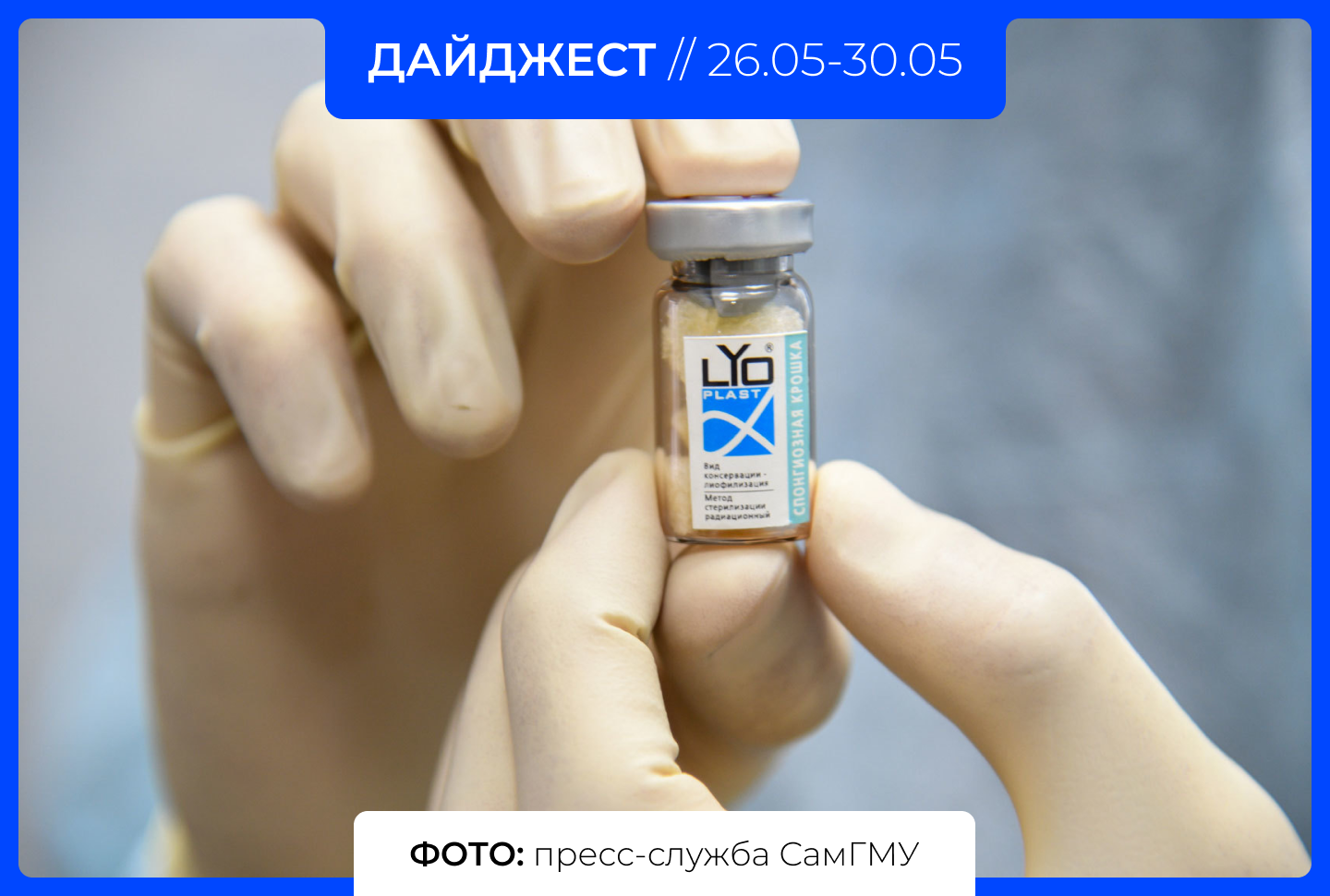
В ПНИПУ изучили метод повышения стойкости 3D печатных металлических деталей к механической усталости
Из-за усталости материала 3D печатные металлические детали могут выходить из строя. Ученые Пермского национального исследовательского политехнического университета нашли способ сделать 3D печатные конструкции прочнее, оптимизировав их обработку и направление печати. Это значительно сократит затраты авиапромышленности на прототипирование и изготовление новых деталей, сообщает пресс-служба вуза на портале Naked Science.
3D печать металлами активно применяется для создания и ремонта изделий, которые трудно сделать обычными методами. В авиации ее используют, например, для изготовления таких деталей, как завихрители камер сгорания. Особенно широкое применение в 3D печати находит титановый сплав ВТ6. Из него изготавливают лопатки турбин, элементы двигателей, облегченные кронштейны и крепления, детали фюзеляжей и шасси, компоненты выхлопных систем, теплообменники.
«При такой методике изготовления есть свои недостатки: в изделиях могут быть дефекты (поры, неравномерная структура), из-за чего материал становится менее прочным. В результате такие детали часто выходят из строя из-за усталости металла. Особенно уязвимы места с концентраторами напряжений, например вырезы или отверстия в местах крепежей для болтов, заклепок и так далее», — рассказал младший научный сотрудник Центра экспериментальной механики ПНИПУ Александр Паньков.
Даже небольшие дефекты поверхности сокращают срок службы авиационных и космических конструкций, поэтому необходимо тщательно изучать, как эти слабые места влияют на конечное состояние деталей. Ученые Пермского политеха провели серию экспериментов с образцами титанового сплава ВТ6, напечатанными на 3D принтере по технологии электродугового наплавления металлической проволоки (WAAM).
«Для проверки прочности мы изготовили образцы и вырезали их в трех направлениях: вдоль, поперек и под углом 45° к слоям печати. Затем провели испытания, имитируя реальные нагрузки в авиации и космонавтике. Сравнили полированные и необработанные образцы, а также модели с односторонними и двусторонними вырезами, в которых скапливаются напряжения. При высоких нагрузках порядка 750 МПа разница между полированными и шероховатыми образцами была минимальна, разрушение начиналось у выреза независимо от полирования. При низких, около 250 МПа, обработанные объекты выдерживали в два-три раза больше циклов. Для промышленности все это означает, что полировка оправдана не всегда: если деталь работает под высокой нагрузкой и проходит регулярные проверки, можно сэкономить на обработке», — рассказал доцент кафедры экспериментальной механики и конструкционного материаловедения Артем Ильиных.
Подробнее: https://3dtoday.ru/blogs/news3dtoday/v-pnipu-izucili-metod-povyseniya-stoikosti-3d-pecatnyx-metalliceskix-detalei-k-mexaniceskoi-ustalosti
3D печать металлами активно применяется для создания и ремонта изделий, которые трудно сделать обычными методами. В авиации ее используют, например, для изготовления таких деталей, как завихрители камер сгорания. Особенно широкое применение в 3D печати находит титановый сплав ВТ6. Из него изготавливают лопатки турбин, элементы двигателей, облегченные кронштейны и крепления, детали фюзеляжей и шасси, компоненты выхлопных систем, теплообменники.
«При такой методике изготовления есть свои недостатки: в изделиях могут быть дефекты (поры, неравномерная структура), из-за чего материал становится менее прочным. В результате такие детали часто выходят из строя из-за усталости металла. Особенно уязвимы места с концентраторами напряжений, например вырезы или отверстия в местах крепежей для болтов, заклепок и так далее», — рассказал младший научный сотрудник Центра экспериментальной механики ПНИПУ Александр Паньков.
Даже небольшие дефекты поверхности сокращают срок службы авиационных и космических конструкций, поэтому необходимо тщательно изучать, как эти слабые места влияют на конечное состояние деталей. Ученые Пермского политеха провели серию экспериментов с образцами титанового сплава ВТ6, напечатанными на 3D принтере по технологии электродугового наплавления металлической проволоки (WAAM).
«Для проверки прочности мы изготовили образцы и вырезали их в трех направлениях: вдоль, поперек и под углом 45° к слоям печати. Затем провели испытания, имитируя реальные нагрузки в авиации и космонавтике. Сравнили полированные и необработанные образцы, а также модели с односторонними и двусторонними вырезами, в которых скапливаются напряжения. При высоких нагрузках порядка 750 МПа разница между полированными и шероховатыми образцами была минимальна, разрушение начиналось у выреза независимо от полирования. При низких, около 250 МПа, обработанные объекты выдерживали в два-три раза больше циклов. Для промышленности все это означает, что полировка оправдана не всегда: если деталь работает под высокой нагрузкой и проходит регулярные проверки, можно сэкономить на обработке», — рассказал доцент кафедры экспериментальной механики и конструкционного материаловедения Артем Ильиных.
Подробнее: https://3dtoday.ru/blogs/news3dtoday/v-pnipu-izucili-metod-povyseniya-stoikosti-3d-pecatnyx-metalliceskix-detalei-k-mexaniceskoi-ustalosti
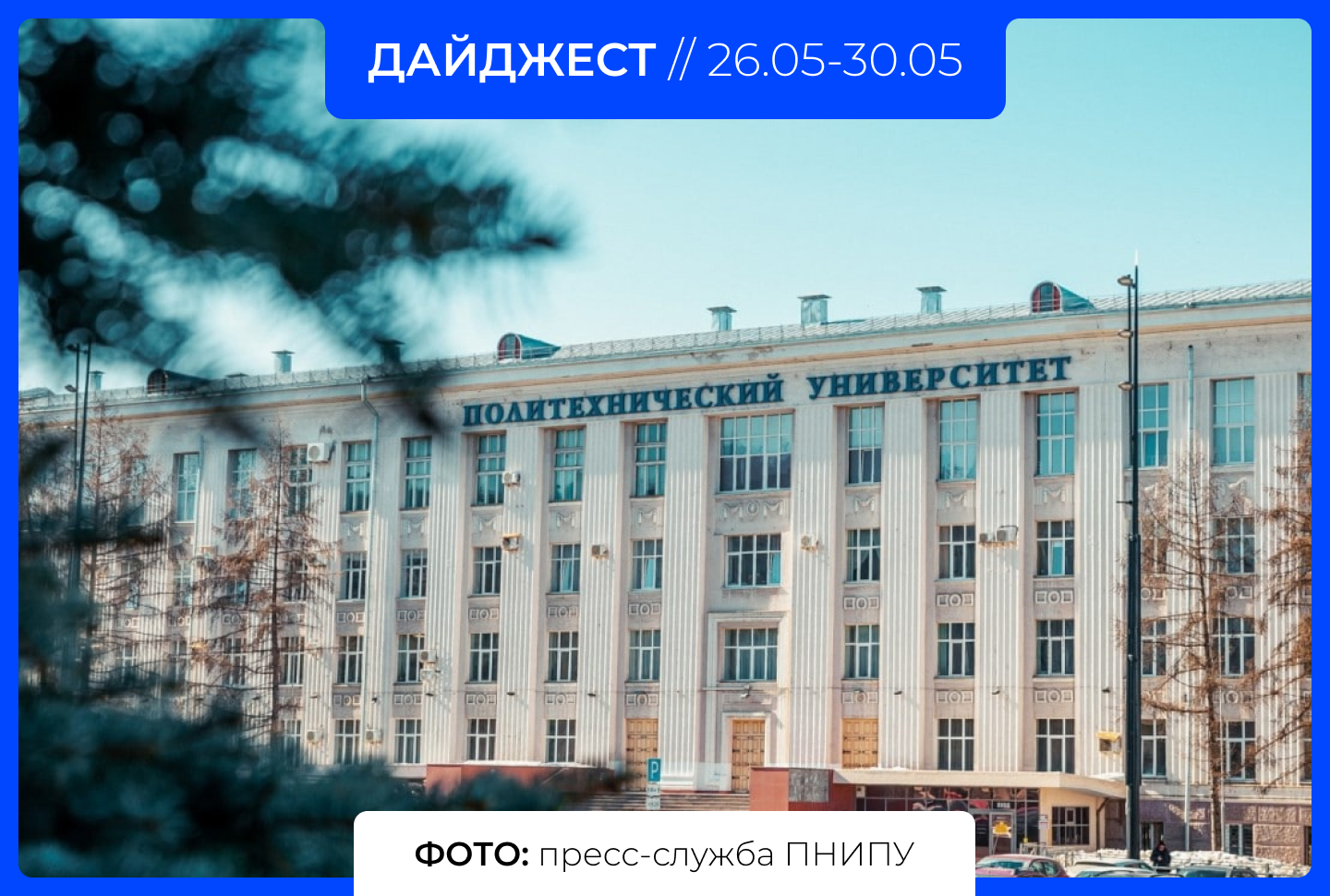
Медицина
Самарские врачи впервые в России установили дентальный имплантат с индивидуальной конструкцией резьбовой части
В Клиниках Самарского государственного медицинского университета пациентке установили индивидуальный дентальный имплантат с индивидуальной конструкцией резьбовой части, оптимизированной под плотность кости. Имплантат изготовлен методом 3D печати.
Обычно пациентам устанавливают имплантаты со стандартной резьбой. Индивидуальная конструкция резьбовой части позволяет не только учитывать плотность костной ткани, но и жевательную нагрузку, пол, возраст и даже хронические заболевания пациентов, что в последующем обеспечивает максимальную приживаемость. Имплантат изготовлен в Научно-исследовательского институте бионики и персонифицированной медицины СамГМУ на 3D принтере по анатомическим параметрам пациентки, сообщает пресс-служба вуза.
Около десяти лет назад 44-летней пациентке удалили зуб. Из-за этого она испытывала дискомфорт, перестала жевать правой стороной, тем самым перегружая височно-нижнечелюстной сустав.
«Так как у женщины наблюдалась резорбция — разрушение костной ткани, обычный имплантат с большой долей вероятности расшатался бы, поэтому для большего контакта и максимальной приживаемости потребовался индивидуальный имплантат. Его изготовили на 3D принтере, предварительно смоделировав длину, диаметр имплантата и площадь контакта с учетом данных плотности костной ткани, жевательной нагрузки, пола, возраста и хронических заболеваний пациента», — рассказала аспирантка НИИ бионики и персонифицированной медицины СамГМУ, врач стоматолог-хирург Анастасия Кийко.
Подробнее: https://3dtoday.ru/blogs/news3dtoday/samarskie-vraci-vpervye-v-rossii-ustanovili-dentalnyi-implantat-s-individualnoi-konstrukciei-rezbovoi-casti
Обычно пациентам устанавливают имплантаты со стандартной резьбой. Индивидуальная конструкция резьбовой части позволяет не только учитывать плотность костной ткани, но и жевательную нагрузку, пол, возраст и даже хронические заболевания пациентов, что в последующем обеспечивает максимальную приживаемость. Имплантат изготовлен в Научно-исследовательского институте бионики и персонифицированной медицины СамГМУ на 3D принтере по анатомическим параметрам пациентки, сообщает пресс-служба вуза.
Около десяти лет назад 44-летней пациентке удалили зуб. Из-за этого она испытывала дискомфорт, перестала жевать правой стороной, тем самым перегружая височно-нижнечелюстной сустав.
«Так как у женщины наблюдалась резорбция — разрушение костной ткани, обычный имплантат с большой долей вероятности расшатался бы, поэтому для большего контакта и максимальной приживаемости потребовался индивидуальный имплантат. Его изготовили на 3D принтере, предварительно смоделировав длину, диаметр имплантата и площадь контакта с учетом данных плотности костной ткани, жевательной нагрузки, пола, возраста и хронических заболеваний пациента», — рассказала аспирантка НИИ бионики и персонифицированной медицины СамГМУ, врач стоматолог-хирург Анастасия Кийко.
Подробнее: https://3dtoday.ru/blogs/news3dtoday/samarskie-vraci-vpervye-v-rossii-ustanovili-dentalnyi-implantat-s-individualnoi-konstrukciei-rezbovoi-casti
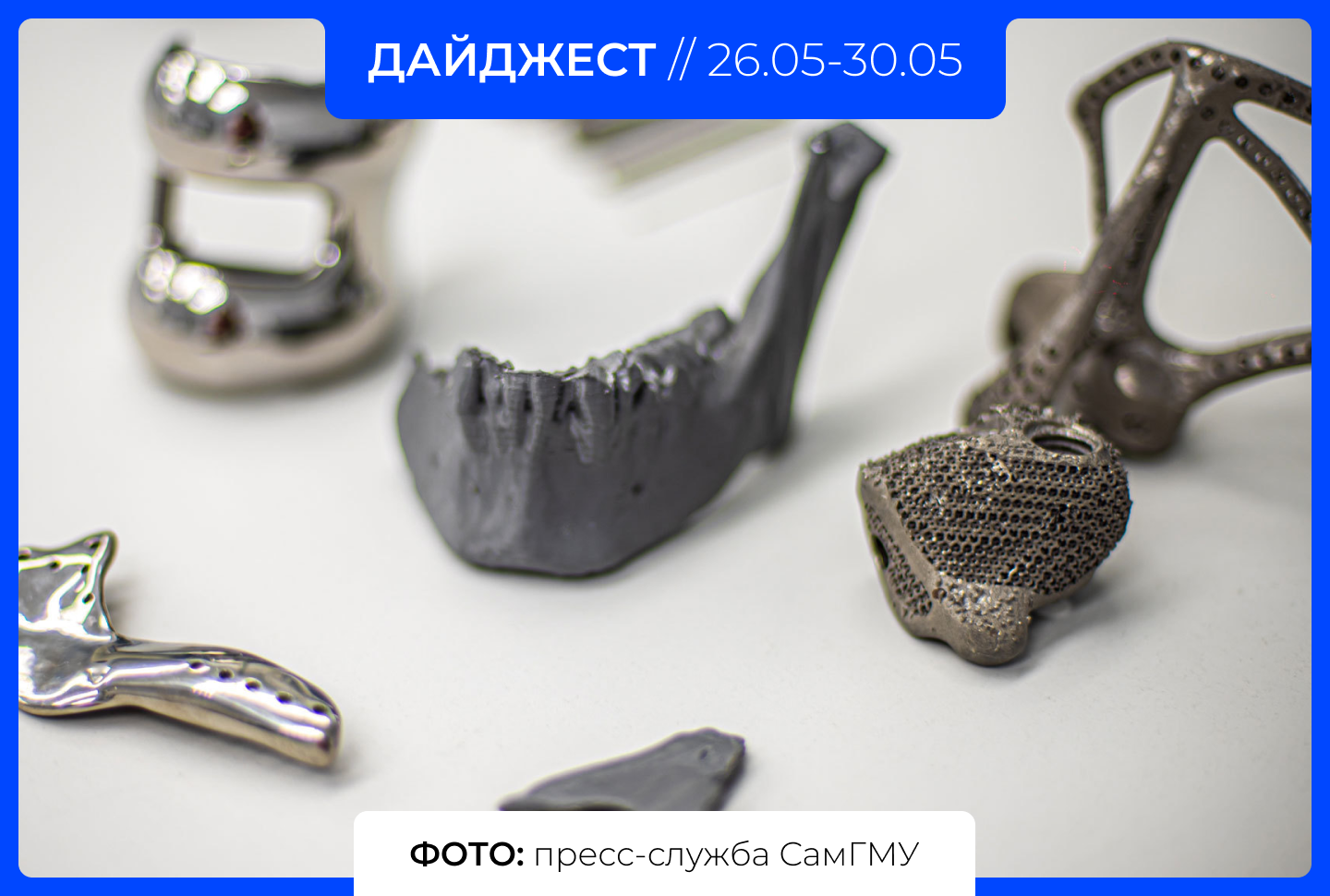
Социальная сфера
РЖД экономит на приборах контроля состояния железнодорожных путей с помощью 3D печати
Электронные путевые шаблоны — инструменты для измерения геометрических параметров железнодорожных путей. Шаблоны тоже со временем выходят из строя, и специалисты Горьковской дирекции инфраструктуры решили обойтись без закупки дорогостоящих новых узлов в пользу ремонта с помощью аддитивных технологий, сообщает отраслевое издание «Гудок».
Оценку исправности таких инструментов дает Нижегородский центр диагностики и мониторинга устройств инфраструктуры. Приборы осматривают и дают заключение о неисправности и необходимости замены того или иного узла. Анализ показал, что часто в негодность приходит дорогостоящий узел шаблона для измерения вертикального износа рельс.
Вместо покупки запасных частей дирекция обратилась к специалистам моторвагонного депо «Канаш». Там есть необходимое аддитивное оборудование и уже освоена 3D печать некоторых запасных частей для рельсовых автобусов. Специалисты Нижегородского центра диагностики и мониторинга устройств инфраструктуры подготовили чертеж детали, отправили его по электронной почте в депо «Канаш» и в скором времени получили запасные части.
Изготовление и установка двадцати узлов собственными силами обошлись примерно в сорок две тысячи рублей, тогда как на покупку заводских запасных деталей пришлось бы потратить около одного миллиона и двухсот тысяч.
Подробнее: https://3dtoday.ru/blogs/news3dtoday/rzd-ekonomit-na-priborax-kontrolya-sostoyaniya-zeleznodoroznyx-putei-s-pomoshhyu-3d-pecati
Оценку исправности таких инструментов дает Нижегородский центр диагностики и мониторинга устройств инфраструктуры. Приборы осматривают и дают заключение о неисправности и необходимости замены того или иного узла. Анализ показал, что часто в негодность приходит дорогостоящий узел шаблона для измерения вертикального износа рельс.
Вместо покупки запасных частей дирекция обратилась к специалистам моторвагонного депо «Канаш». Там есть необходимое аддитивное оборудование и уже освоена 3D печать некоторых запасных частей для рельсовых автобусов. Специалисты Нижегородского центра диагностики и мониторинга устройств инфраструктуры подготовили чертеж детали, отправили его по электронной почте в депо «Канаш» и в скором времени получили запасные части.
Изготовление и установка двадцати узлов собственными силами обошлись примерно в сорок две тысячи рублей, тогда как на покупку заводских запасных деталей пришлось бы потратить около одного миллиона и двухсот тысяч.
Подробнее: https://3dtoday.ru/blogs/news3dtoday/rzd-ekonomit-na-priborax-kontrolya-sostoyaniya-zeleznodoroznyx-putei-s-pomoshhyu-3d-pecati
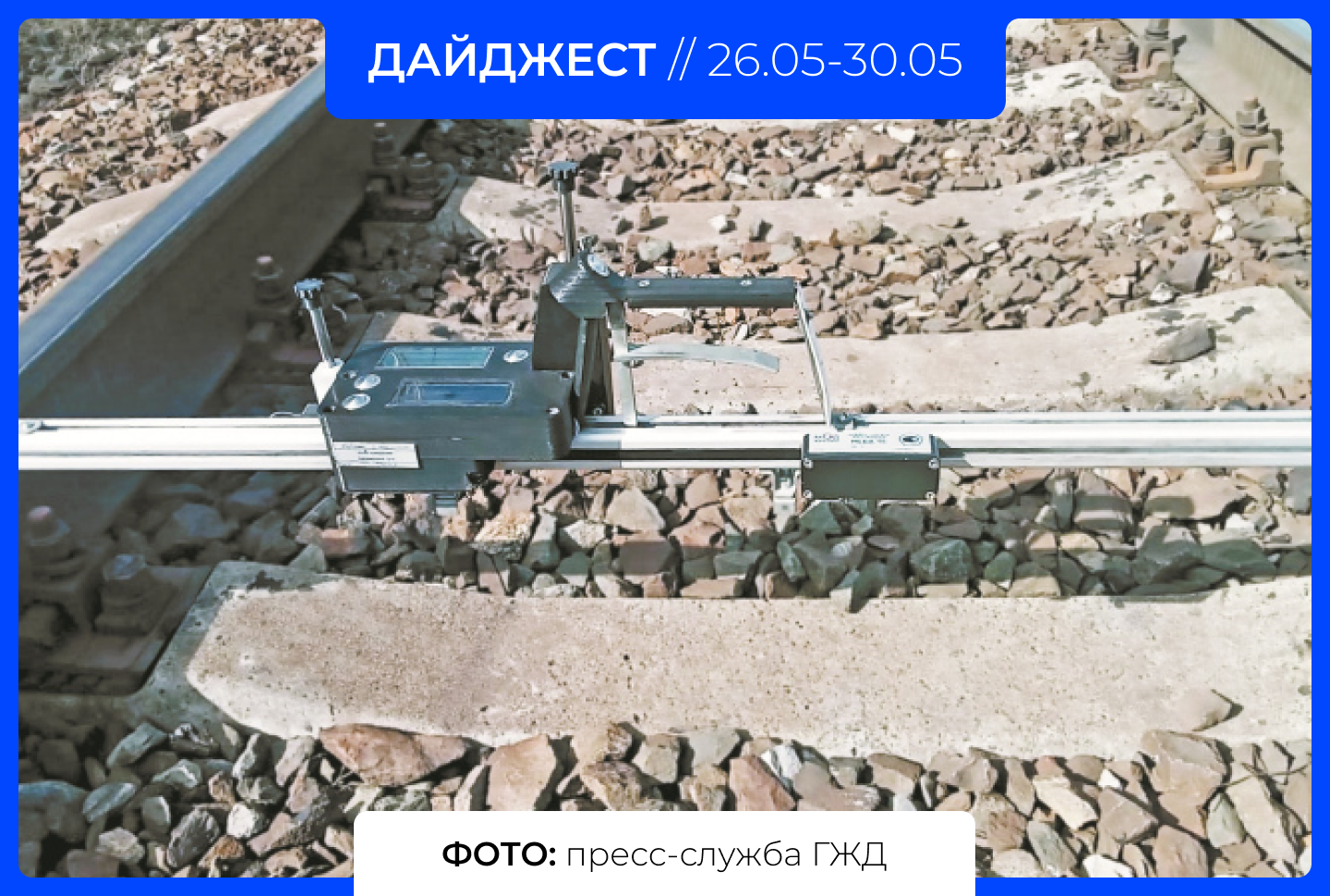
В подмосковном жилом комплексе появился 3D печатный фонтан
Фонтан в жилом комплексе «Римский» Ленинского городского округа стал одним из первых крупных объектов в России, реализованных подобным способом в гражданском строительстве, и одним из самых высоких объектов в Европе, возведенных с применением технологий 3D печати.
«Фонтан высотой двенадцать метров и весом около двадцати тонн изготовлен из цветного бетона с добавлением натуральной каменной крошки. Форма объекта представляет собой стеловую композицию на сферическом основании, расположенную в центре овального бассейна. Фонтан органично интегрирован в общественную зону жилого комплекса и подчеркивает перспективу центрального бульвара, связывая в единую визуальную композицию два многосекционных здания», — сообщает пресс-служба Министерства жилищной политики Московской области.
Более пятидесяти блоков изготовлены на 3D принтере и использованы в качестве несъемной опалубки. Благодаря этому значительно ускорился монтаж сложного архитектурного элемента.
ЖК «Римский» расположен в двух километрах от МКАД по Каширскому и Бесединскому шоссе. Проект выполнен в стиле классического европейского пригорода с элементами итальянской архитектуры.
Подробнее: https://3dtoday.ru/blogs/news3dtoday/v-podmoskovnom-zilom-komplekse-poyavilsya-3d-pecatnyi-fontan
«Фонтан высотой двенадцать метров и весом около двадцати тонн изготовлен из цветного бетона с добавлением натуральной каменной крошки. Форма объекта представляет собой стеловую композицию на сферическом основании, расположенную в центре овального бассейна. Фонтан органично интегрирован в общественную зону жилого комплекса и подчеркивает перспективу центрального бульвара, связывая в единую визуальную композицию два многосекционных здания», — сообщает пресс-служба Министерства жилищной политики Московской области.
Более пятидесяти блоков изготовлены на 3D принтере и использованы в качестве несъемной опалубки. Благодаря этому значительно ускорился монтаж сложного архитектурного элемента.
ЖК «Римский» расположен в двух километрах от МКАД по Каширскому и Бесединскому шоссе. Проект выполнен в стиле классического европейского пригорода с элементами итальянской архитектуры.
Подробнее: https://3dtoday.ru/blogs/news3dtoday/v-podmoskovnom-zilom-komplekse-poyavilsya-3d-pecatnyi-fontan
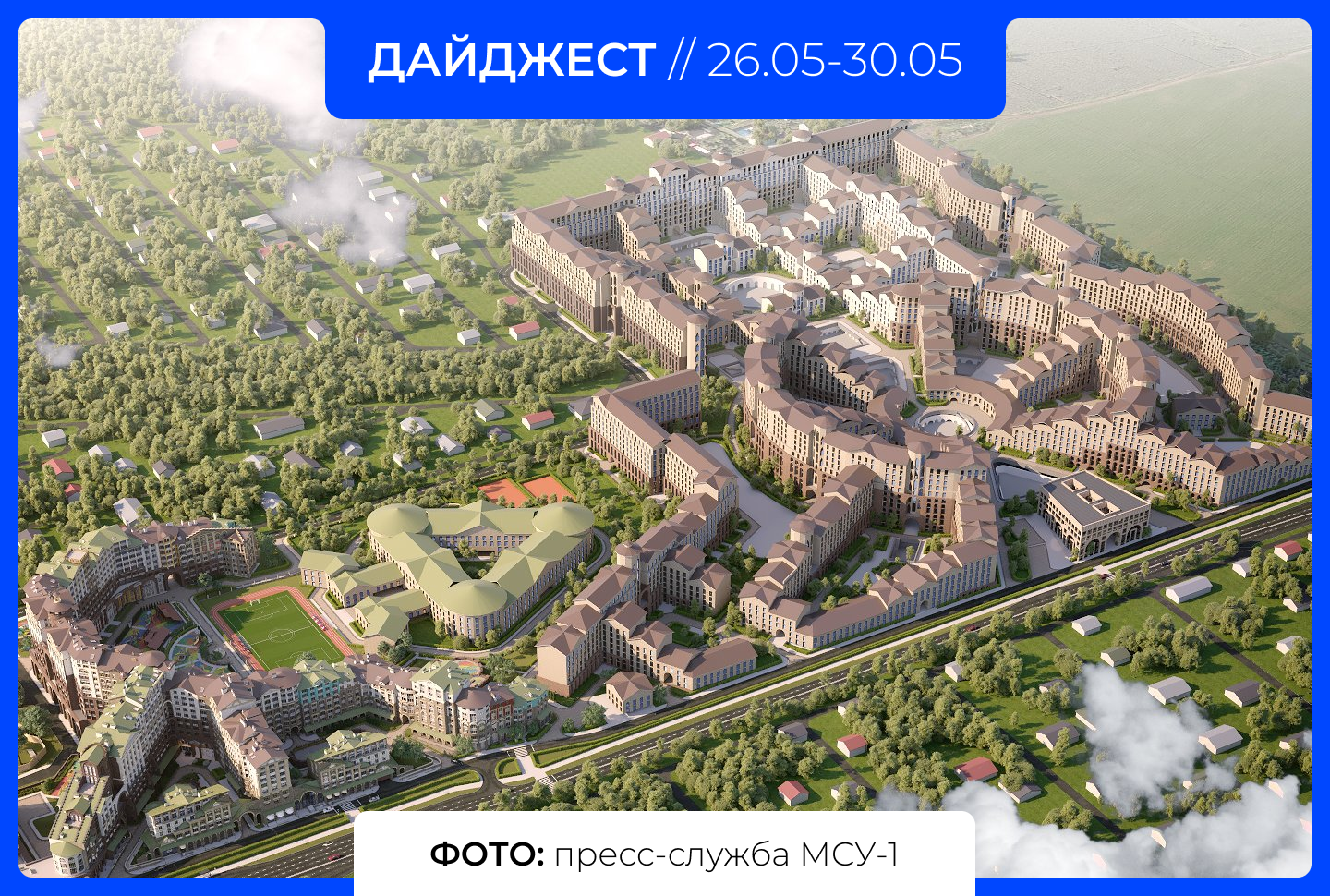
Технологии и развлечения
AirBike — летающий мотоцикл с 3D печатью, который меняет представление о воздушной мобильности
На этой неделе польский стартап Volonaut представил AirBike — летающий мотоцикл. Да, вы не ослышались: это транспортное средство способно парить в воздухе и развивать скорость до 200 км/ч. AirBike, созданный с использованием материалов и деталей, напечатанных на 3D принтере, представляет собой прорыв в области воздушной мобильности, даже несмотря на то, что о его коммерциализации пока известно немного.
Компания Volonaut резюмирует амбиции проекта четким обещанием: «Сделать так, чтобы полеты человека стали возможными». Этот сверхлегкий одноместный летающий скутер, изготовленный из углеродного волокна, является прекрасной иллюстрацией приверженности стартапа технологиям аддитивного производства. В то время как несколько инициатив уже внедрили 3D печать в некоторые детали мотоциклов, AirBike выделяется своей дальновидностью.
Одним из главных преимуществ AirBike является использование аддитивного производства в сочетании с композитными материалами, армированными углеродным волокном. Этот технологический выбор позволил нам создать транспортное средство, которое одновременно является сверхпрочным и чрезвычайно лёгким. По данным Volonaut, AirBike в семь раз легче традиционного мотоцикла благодаря минималистичному подходу и 3D печати.
В отличие от других аппаратов вертикального взлёта и посадки (VTOL), предназначенных для интеграции в городской трафик, AirBike ориентирован на захватывающий и увлекательный опыт. Стартап делает упор на открытое вождение, 360-градусный обзор и компьютерное управление, что даёт пользователю ощущение полной свободы и прямой связи с воздухом.
Подробнее: https://additiv-tech.ru/news/airbike-letayushchiy-motocikl-s-3d-pechatyu-kotoryy-menyaet-predstavlenie-o-vozdushnoy
Компания Volonaut резюмирует амбиции проекта четким обещанием: «Сделать так, чтобы полеты человека стали возможными». Этот сверхлегкий одноместный летающий скутер, изготовленный из углеродного волокна, является прекрасной иллюстрацией приверженности стартапа технологиям аддитивного производства. В то время как несколько инициатив уже внедрили 3D печать в некоторые детали мотоциклов, AirBike выделяется своей дальновидностью.
Одним из главных преимуществ AirBike является использование аддитивного производства в сочетании с композитными материалами, армированными углеродным волокном. Этот технологический выбор позволил нам создать транспортное средство, которое одновременно является сверхпрочным и чрезвычайно лёгким. По данным Volonaut, AirBike в семь раз легче традиционного мотоцикла благодаря минималистичному подходу и 3D печати.
В отличие от других аппаратов вертикального взлёта и посадки (VTOL), предназначенных для интеграции в городской трафик, AirBike ориентирован на захватывающий и увлекательный опыт. Стартап делает упор на открытое вождение, 360-градусный обзор и компьютерное управление, что даёт пользователю ощущение полной свободы и прямой связи с воздухом.
Подробнее: https://additiv-tech.ru/news/airbike-letayushchiy-motocikl-s-3d-pechatyu-kotoryy-menyaet-predstavlenie-o-vozdushnoy
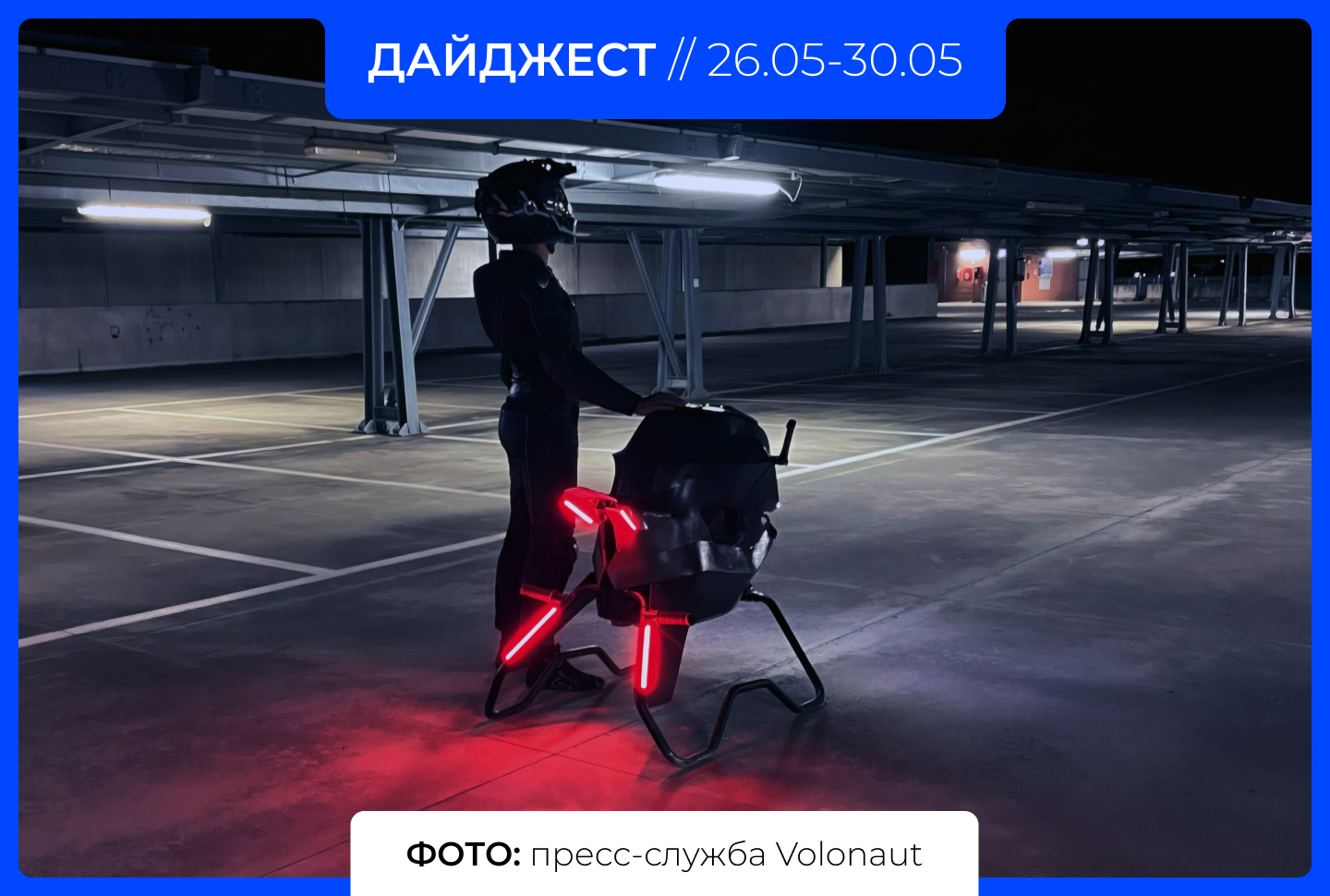